Introduction
Rogers PCBs have become a familiar and essential component in the electronics industry, especially known for their effectiveness in high-frequency applications. These PCBs are far from being a new entry; rather, they are well-integrated into various technological sectors due to their proven performance and reliability.
Specifically, Rogers PCBs are sought after for their low dielectric constant, typically ranging between 2.2 and 3.5, and their high thermal conductivity, often between 0.5 and 2 W/mK. This combination allows for minimal signal loss and superior heat dissipation, making them ideal for high-frequency applications like satellite communications, automotive radar systems, and advanced aerospace electronics. In contrast, traditional FR-4 PCBs, with a higher dielectric constant and lower thermal conductivity, can’t match this level of performance in high-frequency environments.
In the following sections, we delve into the characteristics of Rogers PCBs, highlighting their material composition, key benefits, and the wide range of applications they support.
Unveiling Rogers PCB: Core Attributes and Distinction
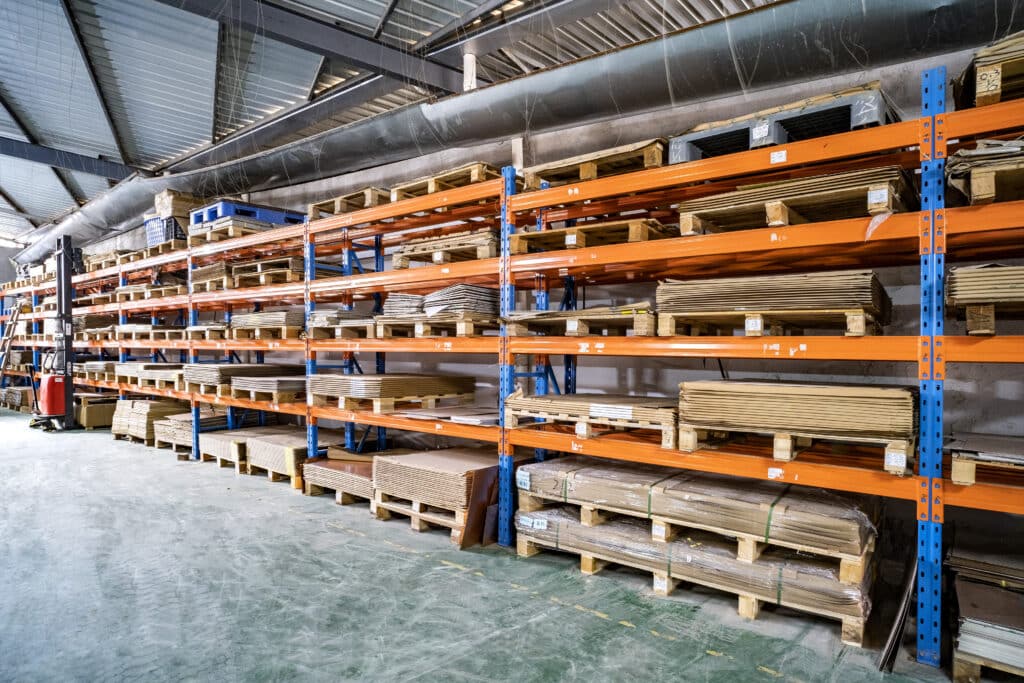
What Are Rogers PCBs?
Rogers PCBs, engineered by Rogers Corporation, are renowned in the electronics sector for their specialized performance in high-frequency applications. These PCBs are the result of sophisticated engineering, involving the lamination of multiple layers of advanced materials. This unique construction endows them with characteristics ideal for high-demand electronic environments:
- Enhanced Signal Integrity: Due to their low dielectric constant, typically in the range of 2.2 to 3.5, Rogers PCBs are adept at preserving signal integrity in high-frequency scenarios. This means clearer and more accurate signal transmission, a critical requirement in many modern electronic devices.
- Reduced Signal Distortion: The low loss tangent, often between 0.001 and 0.002, minimizes signal attenuation and distortion – essential for maintaining the quality and clarity of electronic communications.
- Effective Heat Management: With thermal conductivity values ranging from 0.5 to 2 W/mK, these PCBs can efficiently disperse heat, ensuring stable performance even in high-temperature conditions.
- Stable Under Thermal Stress: The low coefficient of thermal expansion (between 10 and 17 ppm/°C) means that Rogers PCBs remain dimensionally stable even when temperatures fluctuate, an important factor in maintaining long-term reliability.
- Consistent Material Quality: The uniformity in the material structure across these PCBs guarantees consistent performance, an important consideration in complex and precision-dependent electronic systems.
Comparative Analysis: Rogers PCB vs. FR4 Materials
Before diving into the detailed comparison, it’s essential to understand the fundamental distinctions in material composition and application suitability between Rogers PCBs and standard FR-4 materials:
- Material Composition: FR-4, known for its cost-effectiveness and versatility, is a standard choice for many PCBs. However, it falls short in high-frequency performance compared to Rogers materials.
- Suitability for High-Frequency Use: Rogers PCBs are engineered for environments demanding minimal signal loss and phase shift, making them superior in high-frequency applications compared to FR-4.
Building on this foundational understanding, let’s explore more detailed comparisons across various technical aspects:
High-Frequency Performance
- Rogers PCBs: Typically exhibit a dielectric constant around 20% lower than that of FR-4, significantly reducing signal loss at high frequencies.
- FR-4 Materials: Generally have a higher dielectric constant, leading to more signal loss, especially in applications beyond their optimal frequency range.
Dissipation Factor (Df)
- Rogers PCBs: Feature a dissipation factor as low as 0.004, ensuring minimal signal loss. This low Df is crucial in maintaining signal clarity at high frequencies.
- FR-4 Materials: Tend to have a dissipation factor around 0.020, which can increase with frequency, leading to higher signal losses in high-frequency applications.
Impedance Stability
- Rogers PCBs: Offer a wide range of dielectric constants, providing greater flexibility and more stable impedance, especially in variable temperature environments.
- FR-4 Materials: While more cost-effective, they can experience significant variations in dielectric constant with temperature changes, impacting impedance stability. For instance, the dielectric constant of FR-4 can vary greatly, whereas Rogers materials maintain more consistent values across a wide temperature range.
Dielectric Constant
- Rogers PCBs: Possess dielectric constants ranging from approximately 6.15 to 11, higher than those of FR-4 materials. This higher range enables enhanced performance in specific high-energy applications.
- FR-4 Materials: Feature a dielectric constant of about 4.5, making them suitable for general applications where extreme dielectric properties are not required.
Suitability for Space Applications
- Rogers PCBs: Ideal for space applications due to low outgassing properties. For example, their outgassing rates are significantly lower than those of FR-4, making them more stable in vacuum environments.
- FR-4 Materials: Have higher outgassing rates, which can be a limiting factor in space applications.
Temperature Management
- Rogers PCBs: Excel in managing higher temperatures with little variation in performance. They are designed to withstand higher thermal stress, making them reliable in high-temperature applications.
- FR-4 Materials: Are less effective in high-temperature scenarios, with their performance more likely to be affected by temperature fluctuations.
In-Depth Look at Rogers 4350 PCB Series and Dielectric Constant Applications
Rogers 4350 Series: Tailored for High-Frequency Applications
The Rogers 4350 series is a standout in the Rogers PCB lineup, specifically designed to meet the demands of high-frequency applications. Let’s explore why this series is particularly favored in certain sectors:
- Optimized Dielectric Constant (Dk): The RO4350B laminates have a Dk of 3.48 (±0.05), a value that strikes a balance between minimizing signal loss and ensuring signal integrity in high-frequency applications. This makes the 4350 series particularly suitable for microwave and millimeter wave frequencies.
- Low Dissipation Factor (Df): With a Df of 0.0037 at 10 GHz, the 4350 series ensures minimal signal attenuation, crucial for maintaining signal clarity and strength in applications like base station power amplifiers.
- UL 94 V-0 Rated: This rating indicates the material’s flame-retardant properties, adding an extra layer of safety and reliability to its use in various electronics.
Comparative Overview of Rogers PCB Series
To provide context, here’s how the 4350 series compares to other offerings in the Rogers range:
Series | Dielectric Constant (Dk) | Dissipation Factor (Df at 10 GHz) | Key Features | Typical Applications |
---|---|---|---|---|
RO4003C | 3.38 (±0.05) | 0.0027 | Optimized for cost-sensitive Microwave/RF designs | Microwave/RF applications |
RO4350B | 3.48 (±0.05) | 0.0037 | Ideal for base station power amplifier designs, UL 94 V-0 rated | Base station power amplifier designs |
RO4360G2 | 6.15 (±0.015) | 0.0038 | Suitable for applications requiring higher Dk values | High Dk value applications |
RO4000 Series (General) | 2.55-6.15 | Varied | Wide Dk range, thermally robust, FR-4 process compatibility | General high-frequency applications |
Dielectric Constant in Practice: Design Implications
Understanding the dielectric constant is crucial for PCB design:
- What is Dielectric Constant?: It measures a material’s ability to store electrical energy in an electric field. In PCBs, it affects signal propagation and is integral to determining how the board handles electrical signals.
- Impedance Matching: The specific Dk of the Rogers 4350 series influences impedance matching. Correctly matching impedance is crucial for minimizing signal reflections and maximizing signal integrity, especially in RF and microwave circuits.
- Circuit Miniaturization: A higher Dk value, like that of the Rogers 4350 series, enables smaller circuit sizes, beneficial in compact device designs while maintaining efficient performance.
Cost Analysis: Beyond the Price Tag of Rogers PCBs
Understanding the Value of Rogers PCBs in Practical Terms
When considering Rogers PCBs, it’s not just about the higher price; it’s about the value they bring to your projects. Let’s explore this through tangible examples:
Case Study: High-Speed Communication Systems
- Scenario: Imagine you’re developing a high-speed communication system where signal integrity is key. Using standard FR-4 PCBs might seem cost-effective initially, but the signal loss and distortion at high frequencies could lead to inefficient performance and higher long-term costs due to system failures or maintenance needs.
- Rogers PCB Advantage: In contrast, Rogers PCBs, though more expensive upfront, maintain signal integrity even at very high frequencies. For instance, their low dielectric loss means that for a system operating at 10 GHz, signal loss could be reduced by up to 50% compared to standard FR-4 PCBs. This reduction in signal loss translates into a more reliable and efficient system, ultimately saving costs on maintenance and ensuring user satisfaction.
Why Pay More? High-Performance in Automotive Radar Systems
- Application: Consider the use of PCBs in automotive radar systems, which are crucial for safety features like collision avoidance. The reliability of these systems is non-negotiable.
- Cost vs. Benefit: While Rogers PCBs might increase the initial production cost by, let’s say, 15%, they also enhance the radar system’s accuracy and durability. This investment not only improves safety but also reduces the likelihood of costly recalls or legal issues arising from system failures.
ROI from a Business Perspective
- Long-Term Savings: By incorporating Rogers PCBs, a company could see a reduction in warranty claims and maintenance costs. If we quantify this, the use of Rogers PCBs could lead to a 25% decrease in after-sales service costs over the product’s lifetime.
- Enhancing Brand Reputation: Beyond numbers, using high-quality components like Rogers PCBs can bolster a company’s reputation for quality and reliability, which is invaluable in today’s competitive market.
Diverse Applications: The Specific Reach and Rationale of Rogers PCBs
Rogers PCBs are not just versatile; they are critical in a multitude of sectors due to their unique properties. The following table breaks down various industries and specific products where Rogers PCBs are utilized, highlighting the reasons they are the preferred choice in each context:
Industry Sector | Specific Products/Applications | Why? |
---|---|---|
Telecommunications | 5G Network Antennas, Satellite Transceivers, RF Amplifiers, Microwave Links | Preferred for high-frequency performance and signal integrity essential in communication technologies. |
Aerospace | Satellite Communication Systems, Avionic Control Systems, Space Probe Instruments | Chosen for their reliability and thermal stability in extreme space environments. |
Automotive | Collision Avoidance Systems, ADAS, EV Battery Management Systems | Utilized for their durability and high thermal management capabilities in safety-critical systems. |
Medical Technology | MRI Machines, Ultrasound Equipment, Portable Diagnostic Devices | Selected for their precision and reliability in sensitive medical devices. |
Renewable Energy | Solar Power Inverters, Wind Turbine Control Systems, Energy Storage Solutions | Used for their ability to handle high power and maintain stability under varying environmental conditions. |
Scientific Research | Particle Accelerators, High-Resolution Spectrometers, Laboratory Analytical Instruments | Valued for their robustness and precision in advanced scientific equipment. |
Industrial Automation | High-Speed Robotics, Precision Control Systems, Automated Inspection Equipment | Chosen for their reliability and performance consistency in automated operations. |
Consumer Electronics | High-End Audio Systems, Virtual Reality Headsets, Advanced Gaming Consoles | Preferred for their superior signal integrity and performance in high-end consumer electronics. |
Defense & Security | Radar Systems, Secure Communication Devices, Electronic Warfare Equipment | Selected for their reliability and performance in critical defense and security applications. |
Computing & Networking | High-Speed Servers, Data Center Switches, Advanced Routers | Utilized for their ability to handle high-frequency signals and heat management in computing and networking equipment. |
Conclusion
Throughout our exploration, we’ve seen how Rogers PCBs stand apart in the electronics world. Their key attributes – from enhanced signal integrity in high-frequency applications to superior thermal management – make them a preferred choice in various sectors. We delved into their specific advantages over traditional FR-4 materials, especially in demanding environments like aerospace, telecommunications, and automotive industries. By understanding their diverse applications and the technical rationale behind their use, it’s clear that Rogers PCBs are essential for cutting-edge technology and reliable performance.
When it comes to implementing high-performance PCB solutions, Rowsum is your ideal partner. Our expertise in providing high-quality Rogers PCBs and other advanced electronic components positions us to meet your project’s specific requirements. With Rowsum, you gain access to top-tier PCB technology, backed by a commitment to excellence and customer satisfaction. Explore our offerings at www.rowsum.com, and let us support you in achieving technological innovation and success.