Ever been in that nerve-wracking situation where a critical PCB component failed during final testing, throwing your entire production schedule into chaos? Or perhaps you’re an engineer who’s been grappling with inconsistent solder joints and unreliable wire bonds in your consumer electronics project. What if there was a surface finish that could be your silver bullet for these common yet critical issues?
ENEPIG (Electroless Nickel Electroless Palladium Immersion Gold) is a specialized surface finish for PCBs that significantly enhances solder joint reliability, wire bonding, and contact resistance. It serves as a comprehensive solution for industries requiring high reliability and cost-effectiveness, such as medical, automotive, and industrial automation.
Unpacking ENEPIG: More Than Just an Acronym
What Does ENEPIG Stand For?
ENEPIG is an acronym for Electroless Nickel Electroless Palladium Immersion Gold. Each component in this name represents a layer in the ENEPIG finish, and each layer serves a specific purpose that contributes to the overall performance and reliability of the PCB.
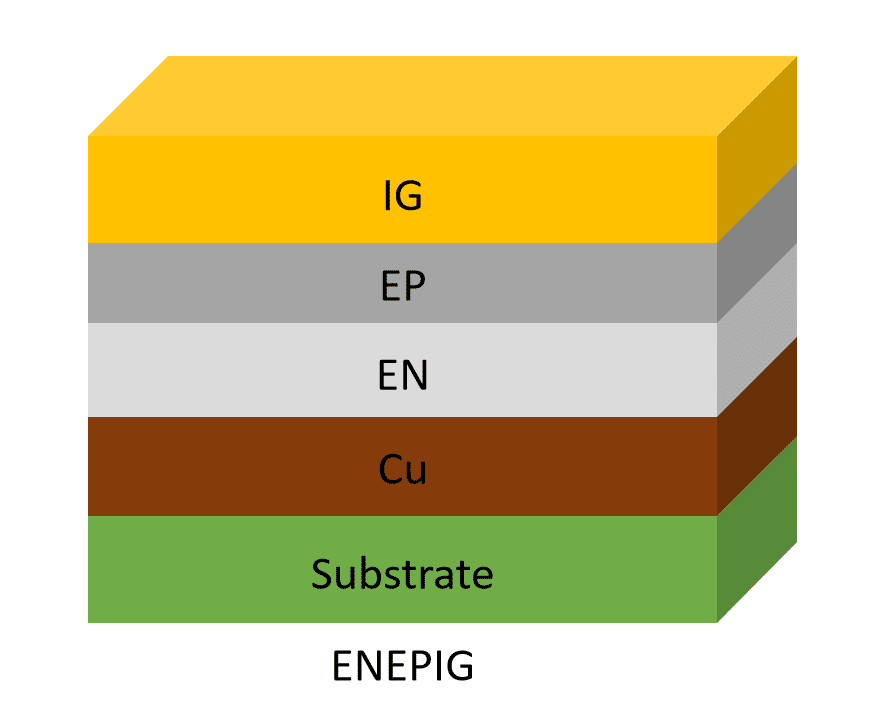
The Layers and Their Functions
Electroless Nickel
The first layer, Electroless Nickel, acts as a barrier to protect the copper surface of the PCB. It provides excellent corrosion resistance and ensures that the solder doesn’t interact directly with the copper, which can lead to solder joint failures.
Electroless Palladium
The second layer is Electroless Palladium. This layer enhances the wire bonding capabilities of the PCB, making it ideal for applications that require strong and reliable connections.
Immersion Gold
The final layer is Immersion Gold, which provides a protective layer over the palladium. It improves the surface’s wettability, ensuring that the solder spreads evenly, which is crucial for reliable solder joints.
Why It’s More Than Just an Acronym
While ENEPIG might initially seem like a complex jumble of words, each element plays a critical role in enhancing the PCB’s performance. It’s a carefully engineered solution designed to address multiple challenges in PCB design and manufacturing, especially in high-reliability sectors like medical, automotive, and industrial automation.
The ENEPIG Revolution: A Process Overview
Why Traditional PCB Surface Finishes Fall Short
Ever wondered why your medical device prototype failed its reliability test? Or why your automotive PCB isn’t performing as expected? Traditional surface finishes like HASL and ENIG might be the culprits. While they have their merits, they often fall short in critical applications.
The ENEPIG Process: What It Solves For You
Pre-treatment: The Foundation of Reliability
Before diving into the ENEPIG layers, it’s crucial to understand the pre-treatment process. This isn’t just a preparatory step; it’s your first line of defense against contaminants that can compromise your PCB’s performance.
Electroless Nickel: More Than a Barrier
The Electroless Nickel layer serves as a barrier and is typically 3.0 to 5.0 microns thick. It prevents copper-solder interactions, reducing the risk of joint failures, especially in medical devices.
Electroless Palladium: The Wire Bonding Maestro
The Palladium layer is typically 0.05 to 0.1 microns thick and ensures robust wire bonding. In automotive applications where vibrations can be an issue, this layer is vital.
Immersion Gold: The Final Touch of Excellence
The Immersion Gold layer, usually 0.03 to 0.05 microns thick, enhances the wettability of your PCB. This is particularly important in industrial automation where soldering efficiency can impact production time.
Why ENEPIG is Your Best Bet
ENEPIG is a comprehensive solution for high-reliability applications in medical, automotive, and industrial sectors. It addresses the limitations commonly encountered with traditional surface finishes.
Key Advantages of ENEPIG
ENEPIG offers a range of benefits that make it stand out:
Corrosion Resistance
Excellent for harsh environments, ENEPIG acts like a protective layer against corrosion.
Long Shelf Life
Beneficial for projects with extended timelines, ENEPIG ensures your PCBs have a longer shelf life.
Cost-Effectiveness
Though initially more expensive, its durability and reliability make ENEPIG a cost-effective choice in the long run.
Compatibility with Multiple Alloys
ENEPIG is compatible with a wide range of solder alloys, offering flexibility in your projects.
Improved Signal Integrity
Ideal for high-frequency applications, ENEPIG enhances signal clarity and performance.
ENEPIG vs The World: A Comparative Analysis
Criteria | ENEPIG | HASL | ENIG | OSP |
---|---|---|---|---|
Corrosion Resistance | Excellent | Good | Very Good | Good |
Shelf Life | Long | Moderate | Long | Short |
Cost | Moderate-High | Low | High | Low |
Solderability | Excellent | Good | Very Good | Good |
Wire Bonding | Excellent | Poor | Poor | Poor |
Signal Integrity | Excellent | Good | Very Good | Good |
Alloy Compatibility | High | Moderate | Moderate | Low |
Textual Explanations:
- Corrosion Resistance: Unlike HASL and OSP, which offer good corrosion resistance, ENEPIG and ENIG are superior in this aspect. ENEPIG takes the lead with excellent corrosion resistance.
- Shelf Life: ENEPIG and ENIG outlast HASL and OSP in terms of shelf life. OSP, in particular, falls short with a short shelf life.
- Cost: While ENEPIG and ENIG are on the higher end of the cost spectrum, HASL and OSP are more budget-friendly but come with limitations in performance.
- Solderability: ENEPIG excels in solderability, outperforming HASL and OSP. ENIG comes close but doesn’t match ENEPIG’s excellence.
- Wire Bonding: ENEPIG is the clear winner here, as HASL, ENIG, and OSP all perform poorly in wire bonding applications.
- Signal Integrity: ENEPIG and ENIG offer better signal integrity compared to HASL and OSP, making them more suitable for high-frequency applications.
- Alloy Compatibility: ENEPIG offers the highest alloy compatibility, making it more versatile than HASL, ENIG, and OSP, which offer moderate to low compatibility.
FAQs: The Questions You Didn’t Know You Had
Q1: How Does ENEPIG Impact Environmental Sustainability?
ENEPIG is RoHS-compliant and doesn’t contain lead, making it an environmentally friendly option. As industries are increasingly focusing on sustainability, choosing ENEPIG aligns with eco-friendly initiatives.
Q2: What Are the Storage Requirements for ENEPIG-Coated PCBs?
ENEPIG-coated PCBs have a long shelf life and don’t require special storage conditions. However, it’s advisable to store them in a dry, cool place to maintain their quality over time.
Q3: How Does ENEPIG Affect Signal Integrity?
Signal integrity is a big deal, especially for high-frequency and high-speed circuits. ENEPIG excels in this department. It provides excellent signal integrity, making it a go-to choice for applications that require high-speed data transmission.
Q4: Can I Use ENEPIG for Wire Bonding?
Absolutely, ENEPIG is a great choice for wire bonding. It offers robust and reliable connections, which is especially important in applications where mechanical vibrations could be a concern.
Q5: Is ENEPIG Compatible with Lead-Free Soldering?
Yes, ENEPIG is fully compatible with lead-free soldering processes. As the industry is moving towards more environmentally friendly solutions, having a surface finish that’s ready for the future is a smart move.
Conclusion
Look, tech waits for no one. If you’re after reliability and cost-effectiveness, ENEPIG is your go-to. It’s not just another layer; it’s your future-proof strategy in PCB manufacturing.
Got questions or ready to make the switch? Shoot us an email at [email protected]. Let’s future-proof your PCBs, together.