Introduction
Are you struggling to understand the differences between IPC Class 1, Class 2, and Class 3 for PCBs, and why it matters for your projects? This is a common question, especially when balancing the need for quality and cost-effectiveness in electronics manufacturing.
IPC classes categorize PCBs based on their quality and reliability requirements. In simple terms, IPC Class 1 is suitable for everyday consumer electronics where cost is a priority and occasional failures are acceptable. IPC Class 2 is for commercial products that need to be more reliable and durable. IPC Class 3 is for high-end, critical devices where failure is not an option, such as in medical or aerospace electronics. Understanding these categories helps ensure that your PCBs align with the specific demands and standards of your project.
The Fundamentals of IPC Class Standards
The Genesis of IPC Standards: Charting the Course of Electronics Manufacturing
The inception of IPC standards is a fascinating tale of foresight and collaboration in the face of rapid technological evolution. In the early days of the electronics industry, manufacturers grappled with diverse production standards, leading to inconsistencies in product quality and performance. Recognizing the need for uniformity, IPC (Institute for Printed Circuits) was established in the 1950s. It brought together industry leaders to develop a set of guidelines that would become the cornerstone of electronics manufacturing. These standards were not just about ensuring quality; they were about setting a global language for innovation and excellence in the electronics industry.
IPC Class 1: The Foundation of Consumer Electronics
- Class 1: Emphasizing Accessibility and Practicality
IPC Class 1 standards are the bedrock of consumer electronics, focusing on products where cost-effectiveness and basic functionality are key. These standards apply to a vast spectrum of everyday gadgets, from battery-operated toys to simple home appliances. Class 1 products, while not designed for harsh environments or prolonged use, are integral in making technology widely accessible. They embody the principle of ‘technology for all’, providing practical solutions to daily needs with an emphasis on affordability and basic performance.
IPC Class 2: The Standard for Enhanced Durability
- Class 2: Balancing Longevity with Consumer Expectations
IPC Class 2 standards cater to a more demanding segment of the electronics market. This class includes devices that are part of our daily lives – laptops, smartphones, and kitchen appliances. These products are expected to offer reliable performance over a significant period. Class 2 standards ensure these devices can endure regular use, offering consumers a blend of durability and value. They represent a commitment to quality that goes beyond the basics, ensuring that everyday electronics are both dependable and accessible.
IPC Class 3: The Pinnacle of Precision and Reliability
- Class 3: Setting the Bar for High-Performance Electronics
IPC Class 3 standards are the epitome of excellence in electronics manufacturing. Reserved for products where failure is not an option, this class encompasses electronics used in critical applications such as in medical life-support systems, aerospace technology, and military operations. These standards demand the highest level of precision, quality, and reliability. Every component under Class 3 must withstand extreme conditions and rigorous testing, reflecting an unwavering commitment to safety and performance. IPC Class 3 is not just a set of standards; it’s a testament to human ingenuity and the relentless pursuit of perfection in technology.
IPC Class | Quality & Reliability Standards | Intended Use |
---|---|---|
Class 1 | Standard quality; suitable for basic functionality and non-critical applications | Consumer products with limited life expectancy |
Class 2 | Enhanced quality; designed for improved performance and extended life | Commercial products where extended life and higher reliability are required |
Class 3 | Premium quality; highest level of reliability for critical applications | Products that must perform reliably in demanding and potentially life-saving situations |
Detailed Design Rule Differences Between IPC Class2 and Class3
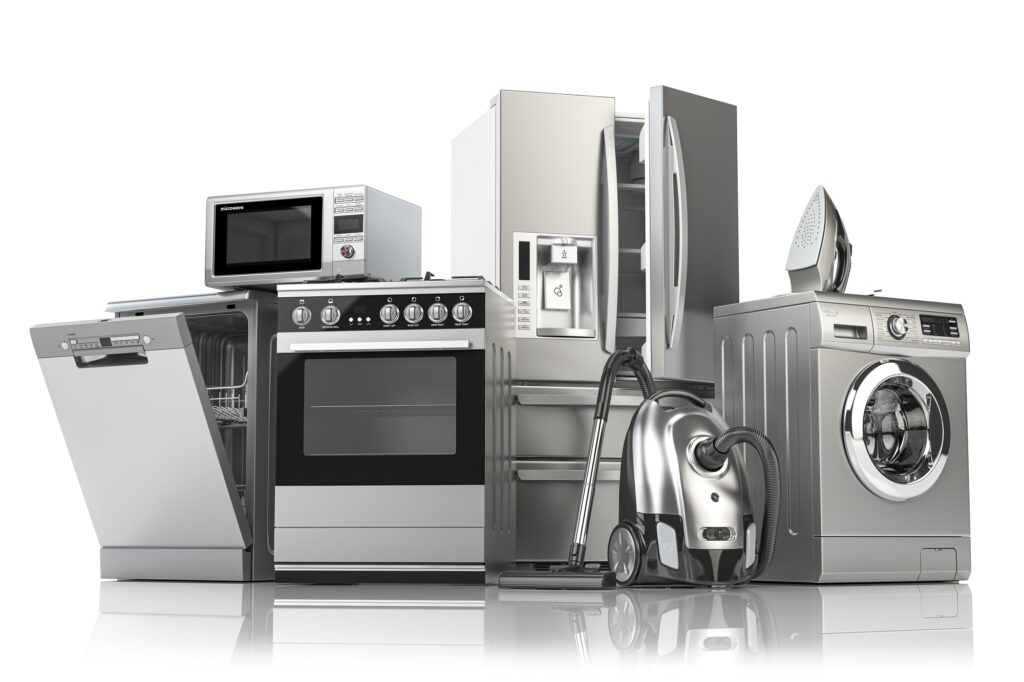
Introduction to the Section:
In the intricate world of PCB manufacturing, discerning the subtle yet significant differences between IPC Class 2 and Class 3 standards is essential for aligning with the diverse demands of quality, reliability, and cost-effectiveness. While IPC Class 1 caters to basic quality requirements typical of general consumer electronics, it’s the Class 2 and Class 3 standards that are more relevant for sectors demanding higher reliability. This section explores the specific design rule differences between these two classes, shedding light on the technical nuances that define their distinct applications.
Trace Widths and Spacing:
- Class 2: Offers flexibility with trace widths and spacing, accommodating a variety of applications where uninterrupted service is preferred but not critical. Typical trace width and spacing might be around 0.010 inches, suitable for standard consumer electronics.
- Class 3: Demands tighter trace widths and spacing for high-reliability electronics, often used in critical applications like medical devices or aerospace. Trace widths could be as narrow as 0.007 inches with equivalent spacing, ensuring superior performance under stringent conditions.
Component Placement and Density:
- Class 2: Allows for moderate component density and more relaxed placement tolerances, balancing performance with cost-effectiveness. Ideal for products where consistent performance is valued.
- Class 3: Requires highly precise component placement and higher density, catering to compact and high-performance needs of critical systems where failure is not an option.
Via Structures:
- Class 2: Designed with robustness in mind, vias in Class 2 PCBs have broader tolerances, aligning with general commercial product requirements.
- Class 3: Features meticulously designed vias with tight tolerances, optimized for maximum reliability in environments where even the slightest failure is unacceptable.
The distinction between IPC Class 2 and Class 3 is pivotal in determining the appropriate level of quality and reliability for different applications. Class 2 strikes a balance suitable for standard commercial products, while Class 3 is tailored for high-reliability applications where performance and precision are paramount. This understanding is key to making informed choices in PCB design and manufacturing, ensuring that the end product aligns with its intended use and environment.
Feature | IPC Class 2 | IPC Class 3 | Remarks |
---|---|---|---|
Trace Widths and Spacing | Standard widths (e.g., 0.010 inches) | Narrower widths (e.g., 0.007 inches) | Class 3 requires tighter spacing for higher density and reliability |
Annular Ring | Minimum 0.002 inches | Minimum 0.003 inches | Class 3 demands a larger annular ring for enhanced durability |
Plated Through-Holes (PTH) | Tolerances allow for some displacement | Stringent tolerances with minimal displacement | Class 3 standards ensure high precision in PTH for critical applications |
Solder Mask | Standard application | More precise application, often with smaller clearances | Class 3 requires a more accurate solder mask for complex designs |
Board Thickness | Standard thickness suitable for general use | Often thicker to accommodate higher layer counts | Class 3 boards are designed for more demanding environments |
Thermal Management | Standard considerations | Enhanced requirements due to higher component density | Class 3 boards often include advanced thermal management solutions |
Extensive Applications: Diverse Products Across IPC Classifications
IPC Class 1 Products: General Use and Disposable Electronics
IPC Class 1 standards cater to products where basic functionality and cost-effectiveness are prioritized over longevity. These products are typically non-critical and disposable. More examples include:
- Disposable Cameras: Single-use cameras for casual photography.
- Electronic Greeting Cards: Cards with simple sound or light features.
- Low-Cost LED Lighting: Basic LED bulbs and decorative lights.
- Throwaway Electronic Tools: Inexpensive calculators, digital thermometers, or battery testers.
IPC Class 2 Products: Enhanced Consumer and Business Electronics
IPC Class 2 standards are applied to products requiring dependable performance and a moderate lifespan. These are commonly used in both personal and business settings. Additional examples include:
- Office Electronics: Printers, scanners, and copiers used in business environments.
- Home Appliances: Microwave ovens, coffee makers, and other mid-range kitchen appliances.
- Personal Audio Devices: MP3 players, portable speakers, and mid-range headphones.
- Business IT Equipment: Workstation computers, monitors, and non-critical servers.
IPC Class 3 Products: Critical Performance and Safety-Dependent Electronics
IPC Class 3 standards are reserved for electronics where failure can have severe consequences. These are essential in high-reliability and safety-critical applications. Further examples include:
- Military and Defense Electronics: Communication devices, surveillance systems, and navigation equipment used in defense applications.
- Aerospace Components: Avionics, satellite systems, and space exploration equipment.
- High-End Medical Equipment: Advanced diagnostic machines like MRI and CT scanners.
- Safety Systems in Energy Sector: Nuclear power plant controls, offshore drilling equipment, and renewable energy system controls.
Conclusion
Diving into the PCB IPC classes is like navigating a sea of intricate standards and fascinating technology. From the straightforward simplicity of Class 1 to the uncompromising reliability of Class 3, each class tells a story of innovation tailored for different needs. It’s been a journey of discovery, not just about PCBs, but about the art of balancing quality and practicality.
In this world of precision and standards, Rowsum stands as a beacon of excellence. We don’t just follow IPC Class 2 and Class 3 standards; we elevate them. For those who value quality and reliability in their PCB projects, Rowsum is more than a choice; it’s a statement. Explore the difference we can make at Rowsum.