Introduction
What factors influence the selection of colors for PCBs, and what roles do these colors play in their functionality and design? In the world of electronics, the color of a Printed Circuit Board (PCB) extends far beyond mere aesthetic value; it is integral to the board’s functionality.
The familiar green layer seen on top of most PCBs is known as the solder mask. This layer is pivotal in defining the PCB’s color and plays a key role in the board’s functionality. It acts as an insulator for the circuit’s copper traces, preventing short circuits and guarding against environmental damage. The choice of green as a standard color is due to its ability to balance cost, manufacturability, and ease of inspection. This color offers excellent contrast, aiding in the detection of faults. Conversely, black PCBs are commonly used in applications where heat dissipation is critical, and white PCBs are preferred in LED applications to improve light reflection and efficiency.
The Role, Composition, and History of Green PCB Ink
The green solder mask, now a staple in PCB design, has a history rooted in the evolution of electronics manufacturing. This distinct green layer, more than just a color choice, is a critical component of PCB functionality. Known technically as a solder mask, it’s made from a specialized polymer – typically an epoxy resin mixed with green pigment. This formulation serves to protect the copper circuits from air, moisture, and potential short-circuiting, while also providing a durable, solderable surface.
In the early days of PCB manufacturing, post World War II, the industry faced challenges with unprotected copper traces. These traces were susceptible to corrosion and damage, leading to frequent failures. The introduction of solder masks in the late 1950s and 1960s marked a significant advancement. However, these initial applications were basic and lacked the precision of modern techniques.
The choice of green was initially a result of material availability and compatibility. Green pigments were among the first that were compatible with the epoxy resins used in solder masks. This color offered excellent contrast against the copper traces and the typically white silkscreen markings, making it easier for technicians to inspect and identify any issues. Furthermore, the green hue was less straining to the eyes, an important factor for technicians working with PCBs for extended periods.
As PCB manufacturing technology advanced, the green solder mask became the industry standard. This standardization was driven by the green mask’s ability to balance cost, manufacturability, and ease of inspection. The widespread adoption of green solder masks led to optimizations in the application process, making it a reliable and economically viable option for PCB manufacturers.
Today, the green solder mask is emblematic of the PCB industry’s history and technological progression. While modern advancements have introduced a variety of solder mask colors, green remains a testament to the industry’s early days of innovation and standardization. It symbolizes the balance between functionality, cost-effectiveness, and manufacturability that is essential in PCB design.
Functional Implications of Color Variations in PCB Design
Green PCBs:
- Advantages:
- Thermal Management: Reliable for Heat Management: Green solder masks are known for their effective heat resistance, making them suitable across diverse applications.
- Streamlined Production: Their common use in the industry has led to manufacturing processes being finely tuned for green PCBs, enhancing production efficiency.
- Disadvantages:
- Aesthetic Uniformity: They may lack distinctiveness in products where unique design is a key factor.
- Typical Use: Dominant in a wide array of electronic devices, particularly where balancing cost and reliable performance is essential.
Blue PCBs:
- Advantages:
- Aesthetic Differentiation: Offers a visually distinct alternative, suitable for consumer products where appearance is a factor.
- Moderate Heat Resistance: Generally provides a balance between visibility and thermal performance.
- Disadvantages:
- Variable Inspection Ease: In certain light conditions, the contrast may not be as effective as green PCBs for fault detection.
- Typical Use: Blue PCBs are often used in hobbyist electronics and educational kits, such as certain models of Arduino, where visual appeal is important.
Red PCBs:
- Advantages:
- High Visibility for Components: Good contrast for component placement, which can be beneficial in complex designs.
- Distinct Appearance: Offers a bold and unique look for consumer-facing products.
- Disadvantages:
- Heat Absorption: Can absorb more heat, potentially affecting components in high-temperature environments.
- Typical Use: Red PCBs are commonly found in high-performance computing and gaming hardware, where both aesthetics and component visibility are important.
Black PCBs:
- Advantages:
- Aesthetics: Provides a sleek and premium appearance, ideal for high-end electronics.
- Heat Dissipation: Good for applications with higher thermal loads due to better heat absorption.
- Disadvantages:
- Inspection and Repair Challenges: Lower contrast with traces and pads can hinder defect identification.
- Typical Use: Black PCBs are typically used in advanced consumer electronics such as smartphones and luxury sound systems, where design and heat management are critical.
White PCBs:
- Advantages:
- Reflectivity: Excellent for LED applications as it enhances light efficiency.
- Modern Look: Suited for devices where the PCB is a part of the aesthetic appeal.
- Disadvantages:
- Maintenance: More prone to visible staining and requires careful handling during assembly.
- Typical Use: Commonly used in LED lighting solutions and decorative electronics where the PCB contributes to the overall design and light effectiveness.
Yellow PCBs:
- Advantages:
- High Visibility and Contrast: Yellow solder masks offer excellent visibility, with a high contrast between the solder mask and the copper traces. This feature makes them suitable for PCBs requiring detailed inspection.
- Aesthetically Pleasing: Provides a bright and distinct appearance, which can be advantageous for consumer-facing products where visual appeal is a factor.
- Disadvantages:
- Silkscreen Visibility: Yellow PCBs can present challenges in silkscreen readability, especially if traditional white ink is used.
- Typical Use: Yellow PCBs are often employed in specialized electronics where visual differentiation is important, such as in certain educational or experimental kits.
Purple PCBs:
- Advantages:
- Unique Aesthetic Appeal: Offers a unique and vibrant look, setting them apart from more traditional colors.
- Good Contrast with Silkscreen: Provides reasonable contrast for component labeling and trace visibility.
- Disadvantages:
- Cost and Availability: Often more expensive and less readily available than other colors due to their unique pigment requirements.
- Typical Use: Purple PCBs are sometimes used in custom or niche electronic products, such as DIY electronics or small-scale manufacturing, where a distinct visual identity is desired.
Color | Key Advantages | Notable Disadvantages | Common Usage in Products |
---|---|---|---|
Green | Best for inspections, industry standard | Too common for unique applications | Consumer electronics like TVs, computers, home appliances |
Blue | Striking visual appeal, good heat management | Lower inspection visibility than green | DIY electronics projects, educational robotics kits |
Red | Vivid look, component differentiation | Higher heat absorption | Gaming consoles, high-end graphics cards |
Black | Sleek aesthetics, enhanced heat absorption | Difficult to inspect | Premium audio equipment, advanced smartphones |
White | Reflective (ideal for LEDs), modern appearance | Higher maintenance, discoloration risk | LED light strips, modern smart home devices |
Yellow | Excellent visibility and contrast, eye-catching | Silkscreen readability issues | Specialized test equipment, prototype boards |
Purple | Unique, distinctive for branding | Higher production costs, less availability | Custom IoT devices, limited-edition consumer electronics |
Selecting Colors Based on Project Needs – Tailoring Your Choice to the Application
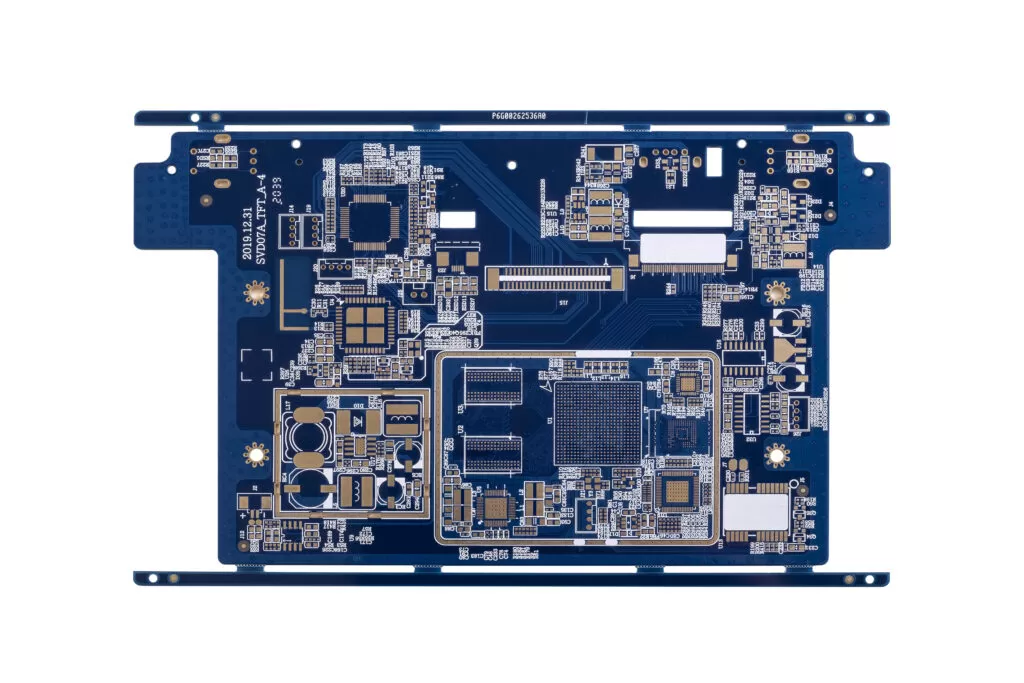
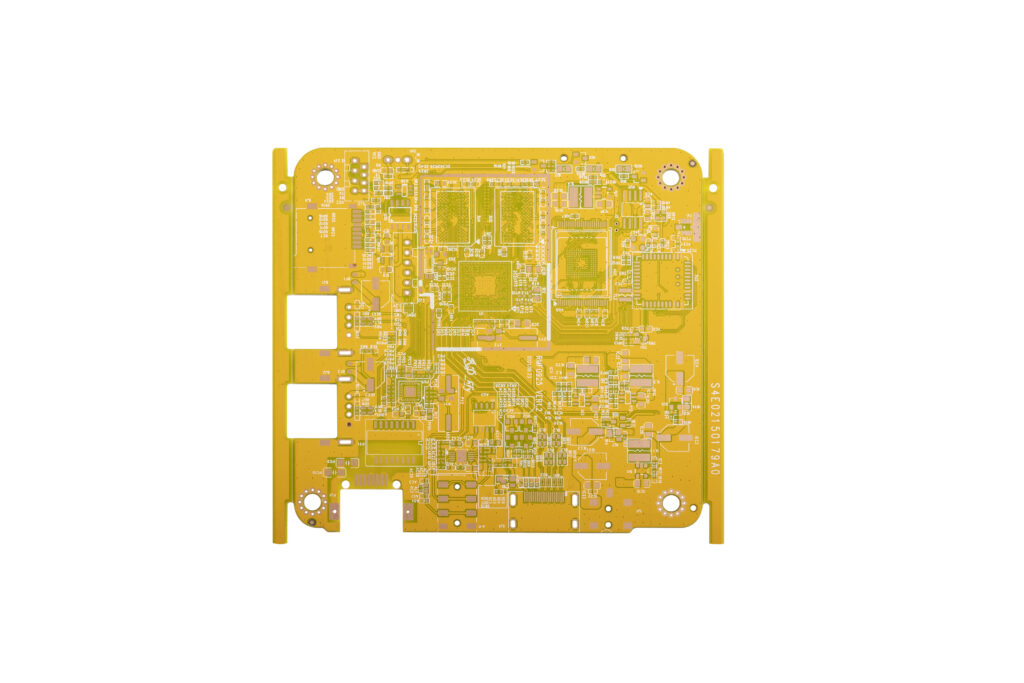
When it comes to choosing the appropriate solder mask color for your PCB, it’s essential to consider the specific needs of your application. This decision should balance functional requirements, cost, and aesthetics. Here’s a guide tailored to various PCB types:
Assess Application-Specific Needs:
- LED PCBs: Opt for white solder masks due to their excellent reflectivity, enhancing the efficiency and brightness of LEDs.
- High-Performance Electronics: Black is ideal where heat dissipation is critical, as it absorbs heat effectively.
- Consumer Electronics: For products where the PCB is visible, such as certain gadgets, vibrant colors like blue and red can align with the product’s aesthetic design.
- Industrial and Automotive: Green is a robust option for its durability and cost-effectiveness, while black can be chosen for its heat resistance.
- Medical Devices: Green and yellow solder masks provide the visibility and contrast needed for intricate designs and inspections, essential in medical applications.
Consider Cost and Manufacturing Efficiency:
- Green: Offers economic benefits due to its widespread use, leading to optimized and cost-effective manufacturing processes.
- Others (Yellow, Red, Purple): These colors might entail higher costs and potentially lower production efficiency due to less standardization.
Visibility and Inspection Needs:
- High Contrast: Green and yellow are excellent for detailed inspections and intricate circuit designs, providing superior visibility.
- Automated Inspection Systems: Systems often optimized for green PCBs can be more efficient due to the color’s high contrast and familiarity in the industry.
Aesthetics and Branding:
- Unique Brand Identity: If the PCB contributes to the product’s visual appeal, selecting a unique color like blue, red, or purple can enhance the overall design and align with brand identity.
Quick Decision Guide:
- Standard and General Electronics: Green is the go-to choice for its balance of cost, efficiency, and functionality.
- LED and Light-Centric Products: White enhances light reflection, making it a preferred choice.
- High-End Consumer Electronics: Black offers a premium look and is suitable for products requiring efficient heat management.
- Specialty Electronics: Yellow or purple can be selected for their distinctive appearance and specific design needs.
By carefully considering these factors, you can select a PCB solder mask color that not only meets the technical requirements of your project but also aligns with the design and branding goals of your product. The ultimate choice should complement your project’s objectives, be it cost-efficiency, performance optimization, or design aesthetics.
Conclusion
As we’ve seen, the choice of PCB solder mask color is more than a cosmetic preference; it’s a strategic decision that influences functionality, inspection ease, and product aesthetics.
At Rowsum, we understand the significance of these choices. That’s why we offer a spectrum of PCB colors to meet your project’s specific needs: green, white, black, red, yellow, purple, and blue. Whether you’re looking for the practicality of green, the reflectivity of white for your LED projects, the sophistication of black, or the vibrancy of other colors, we have the capabilities to bring your design to life with precision and quality.