- Have you ever wondered what makes your electronic devices tick? What’s the secret sauce that powers your smartphones, laptops, and IoT gadgets? Could it be the unsung hero, copper foils, that hold the key to exceptional PCB performance?
Copper foils play a significant role in determining the overall quality, reliability, and performance of a PCB. They are the primary conductive material used in PCBs, and their thickness, quality, and purity directly impact the board’s electrical and thermal properties. Are you intrigued to learn more about the potential of copper foils? Let’s dive in!
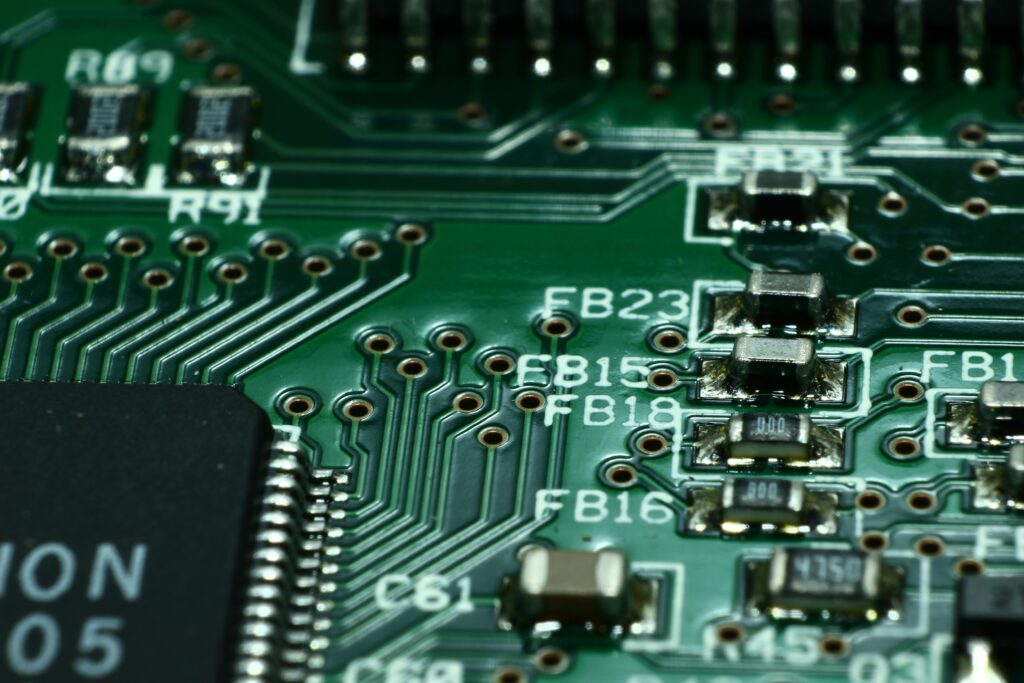
Why is copper foil so important for PCB performance?
Copper foils are responsible for creating the conductive pathways that facilitate the flow of electric current in a PCB. The thickness of the copper layer, also known as copper weight, impacts the board’s ability to handle high currents, heat dissipation, and signal integrity. A higher copper weight translates to better performance, especially in high-power applications 1.
The purity of copper foils is another crucial factor in determining PCB performance. High-purity copper minimizes the presence of impurities and surface defects, ensuring better electrical conductivity and lower signal loss. Industry standards require a minimum of 99.8% pure copper for PCB manufacturing 2.
What are the challenges of using copper foils in PCBs?
Copper foils are not without their challenges. As the demand for smaller, more compact devices continues to grow, PCBs need to accommodate increasingly complex designs and high-density interconnects. This demands thinner copper foils, which can lead to increased electrical resistance and potential signal degradation 3.
Another challenge associated with copper foils is their susceptibility to oxidation, which can negatively affect the adhesion of solder mask and other surface finishes. To prevent this, manufacturers often use surface treatments or protective coatings on copper foils before the PCB assembly process.
How can we optimize copper foil usage for the best PCB performance?
To unlock the full potential of copper foils in PCBs, manufacturers must carefully consider factors such as thickness, purity, and surface treatment. This involves selecting the right copper weight for the specific application, ensuring high-purity copper, and applying appropriate surface treatments to prevent oxidation and improve solderability.
Furthermore, innovations like embedded copper coin technology [^4^] can help enhance the thermal and electrical performance of PCBs, especially in high-power applications. Manufacturers should stay updated on the latest advancements in copper foil technology to create PCBs that deliver optimal performance.
Conclusion
In conclusion, copper foils indeed play a critical role in unlocking the ultimate PCB performance. By carefully considering the factors like thickness, purity, and surface treatment, manufacturers can create high-quality PCBs that meet the demands of today’s fast-paced, technologically advanced world.