Do you often wonder about the actual costs involved in a PCB project? Are you looking for a way to get a reliable estimate upfront? Interested in understanding the factors that can affect your overall PCB costs?
The cost of a PCB can vary widely, but for a concrete example, consider a 50x50mm 2-layer board that could cost as low as $0.15. The formula to calculate this is straightforward: PCB Length x PCB Width x Cost Per Square Meter = Final Price. Keep in mind that the complexity of the board, craftsmanship, and any special requirements can significantly impact the total cost. In essence, the larger the board, the higher the cost. This guide will delve into these nuances to give you a comprehensive understanding of PCB cost estimation.
The Importance and Factors of Accurate PCB Cost Estimation
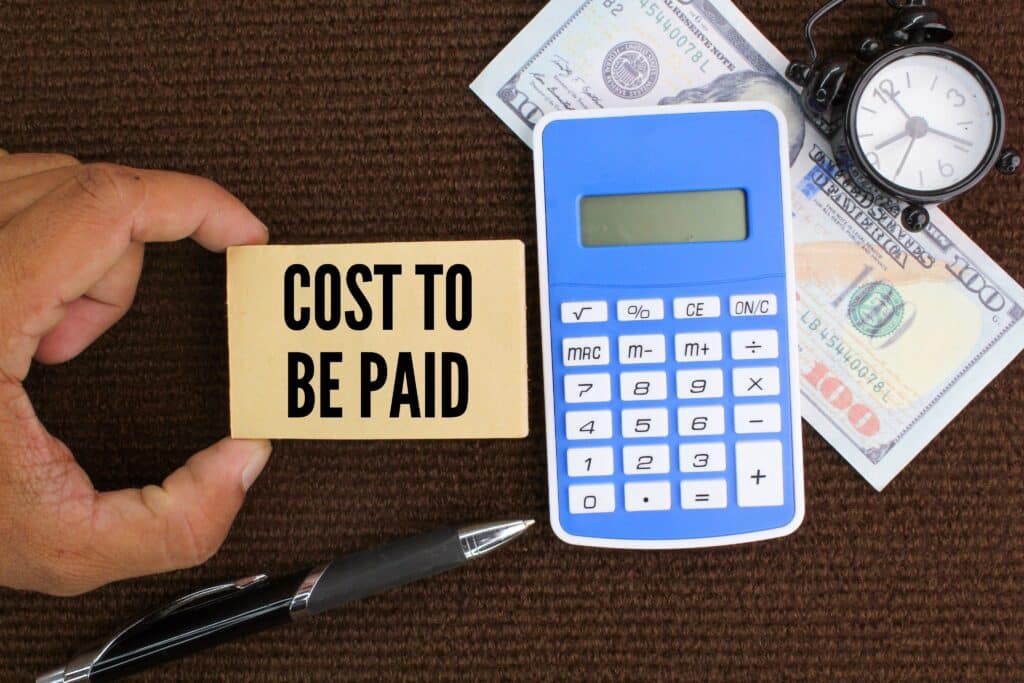
Look, getting the cost of your PCB project spot-on isn’t just some minor detail you can brush off. It’s the backbone of your whole operation. Mess it up, and you’re looking at budget overflows, delayed timelines, and a whole lot of stress. Nail it, and you’re not just saving time and money—you’re also getting a leg up on the competition. So, what’s the secret sauce that goes into this cost?
Comprehensive Factors Influencing PCB and PCBA Cost
Alright, let’s get into the nitty-gritty. You’ve got to understand the whole picture when it comes to the cost of PCB and its assembled version, PCBA. Here’s the lowdown:
Factors Influencing PCB Cost
- Board Size and Complexity: Larger and more complex boards naturally cost more.
- Materials Used: The type of material can significantly impact the cost. For example, FR4 is generally cheaper than Aluminum.
- Layer Count: More layers mean more materials and labor, increasing the cost.
- Special Requirements: Features like blind vias or heavy copper layers can add to the cost.
- Volume of Production: Economies of scale can reduce the unit cost when ordering in bulk.
- Geographic Location: Labor and material costs can vary depending on where the board is manufactured.
Factors Influencing PCBA Cost
- Design Complexity: Advanced designs with intricate features tend to cost more.
- Order Details: The size of your order and how quickly you need it can swing the price.
- Quality Measures: The types of tests and compliance standards your assembly must meet can add up.
- Strategic Costs: This includes labor, materials, and even the sustainability practices of your assembly process.
Hey, if you’re looking to save some cash on your PCBA, I’ve got just the thing for you. Take a peek at these cost-saving tips. Trust me, it’s worth a look.
How to Use a PCB Cost Estimator: Avoid Common Mistakes and Tips for Accuracy
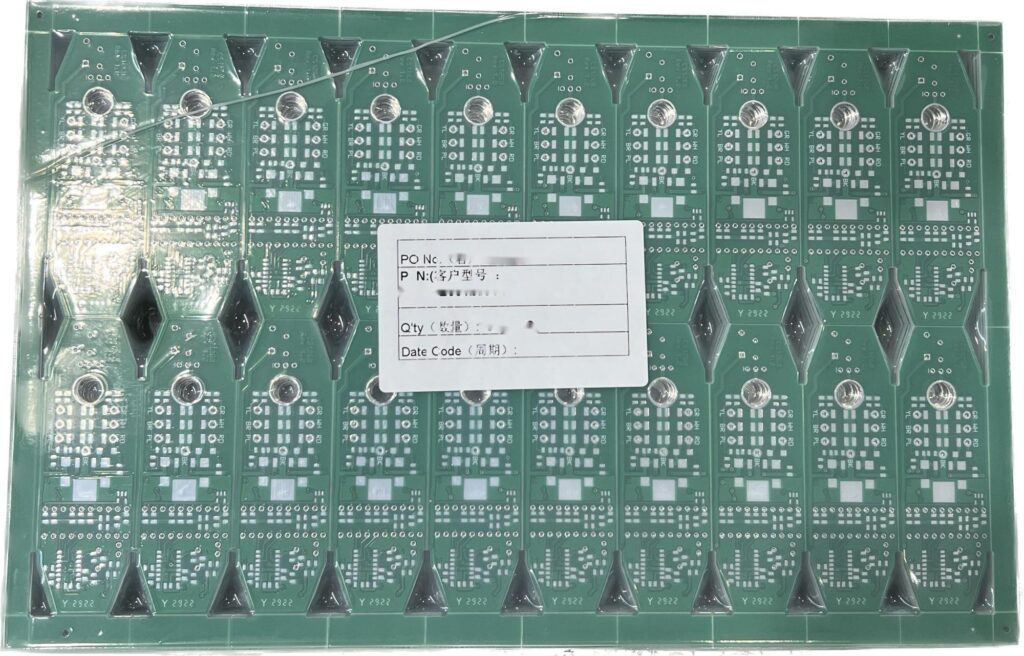
The Reality of Online PCB Cost Estimators
Let’s get real for a second. Online PCB cost estimators are super handy for quick quotes on small batches or prototypes. But here’s the catch: they’re not always accurate for bulk orders. Why? Because these calculators usually work with the dimensions of a single PCB unit.
The Limitation of Single-Unit Calculations
When you upload your design file to a supplier for a quote, it’s usually just for a single PCB. These calculators then spit out a price based on that. But when you’re looking at bulk orders, the game changes. Suppliers will optimize the board layout to maximize material usage. They might even add working edges for easier assembly. So, the dimensions—and therefore the cost—for bulk orders can be quite different.
Step-by-Step Guide to Using a PCB Cost Estimator Formula
Calculating PCB costs doesn’t have to be a mystery. Sure, online tools are convenient, but knowing the math behind the numbers gives you the upper hand. Here’s a simple formula to get you started:
PCB Unit Price = (Length x Width / Number of Boards if Panelized) x Cost Per Square Meter
The Unit Conversion Challenge
Hold on, though! Before you plug in those numbers, let’s talk units. PCB dimensions are usually given in millimeters (mm) or inches, while the cost is often quoted per square meter. So, you’ll need to convert your units to match.
- If your dimensions are in mm: To convert square millimeters to square meters, simply divide by 1,000,000. For example, if your board is 100 mm x 100 mm, that’s 10,000 square mm. Divide that by 1,000,000, and you get 0.01 square meters.
- If your dimensions are in inches: To convert square inches to square meters, multiply by 0.00064516. So, if your board is 4 inches x 4 inches, that’s 16 square inches. Multiply that by 0.00064516, and you get approximately 0.0103 square meters.
Once you’ve got your units aligned, you can proceed with the formula to get a more accurate cost estimate.
Putting It All Together: A PCB Cost Example
Let’s dive into a practical example to make all this math a bit more digestible. I’ll show you a PCB panel image, and we’ll work through the cost estimation together.
PCB Single Unit Dimensions:
The dimensions of a single PCB unit are 143.43 mm x 89.38 mm, and the cost per square meter is $55.
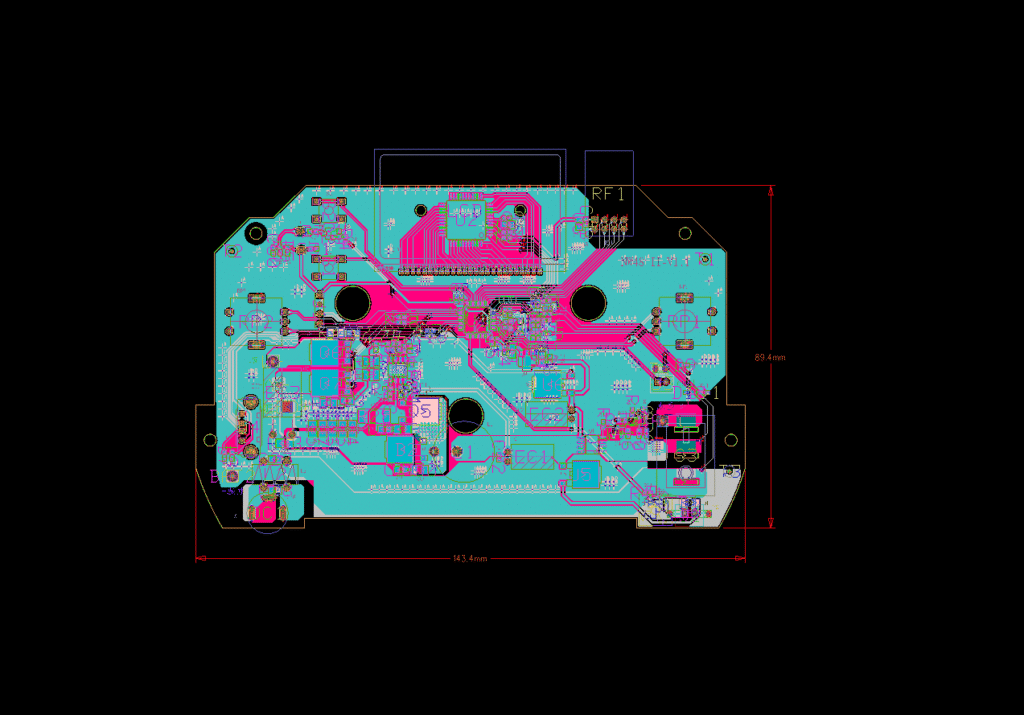
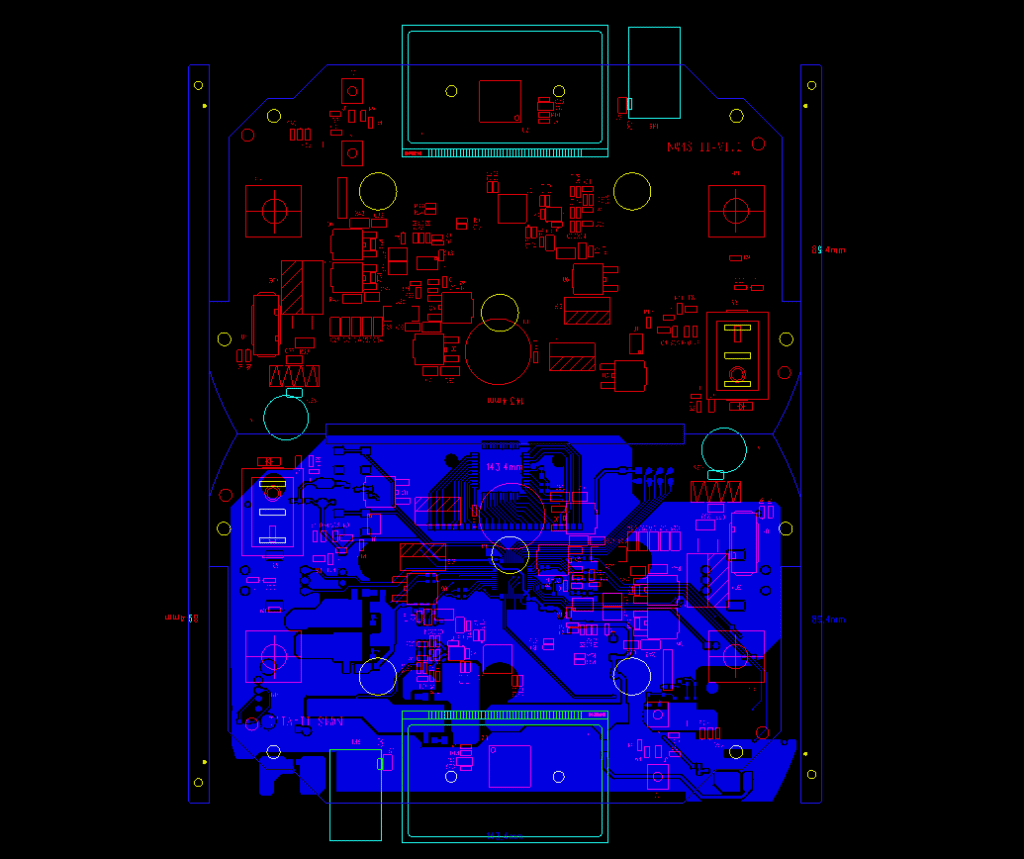
Panelized Dimensions for Bulk Production:
To optimize for bulk production, we panelize the board into a two-unit array and add working edges. The new dimensions become 153.43 mm x 178.76 mm, divided by 2 (with 5 mm working edges on both sides).
Cost Estimation for Single PCB Unit:
If you were to upload this single unit file to most online PCB cost estimators, the unit cost would be calculated as follows:
143.43 mm x 89.38 mm x $55 / 1,000,000 = $0.705 per unit.
Note: This is only applicable for single PCB units, not for bulk orders.
Cost Estimation for Bulk Production with Panelization:
For bulk production, you’ll need to calculate based on the panelized dimensions:
153.43 mm x 178.76 mm / 2 x $55 / 1,000,000 = $0.754 per unit.
Addressing Common Questions
You might be scratching your head, thinking, “Why the fuss about panelizing boards and adding working edges?” Or, “How do I even find out the cost per square meter?” Let’s clear the air.
The Importance of Panelization
Panelization isn’t just a fancy term; it’s a real money-saver. If manufacturers went the route of producing each board individually, labor costs would skyrocket. By panelizing, they can churn out multiple boards in one go, slashing both time and labor costs. That’s a win-win for everyone involved.
Finding Out the Square Meter Cost
Wondering about the cost per square meter? Just hit up your supplier. They’ll spill the beans, and you’ll be all set to make a more accurate cost estimate.
How to Save Costs on Your PCB Projects
So, you’ve mastered the art of calculating PCB costs—what’s the next step? Let’s talk about optimizing those costs. While I’ve previously written an article outlining 11 comprehensive tips for cost-effective PCB manufacturing, here I’ll focus on some key insights that are particularly impactful. For a deep dive into all 11 tips, you can explore my article on PCB Cost-Saving Tips.
Personal Insights on Cost-Saving:
- Keep It Simple, Smarty (KISS): Complexity is the enemy of both your wallet and your peace of mind. A straightforward design can save you a lot of headaches and cash.
- Less Is More: When it comes to components, think minimalism. The fewer parts you have, the less you’ll spend. It’s that simple.
- Stick to the Standards: Custom shapes are cool, but they can burn a hole in your pocket. Stick to standard shapes and sizes to keep costs down.
- Panelization Is Your Friend: Think of it as buying in bulk; it’s cheaper. Panelizing your design can lead to significant savings.
- Embrace the Future: Don’t shy away from using advanced tech tools. They might seem expensive upfront, but they’ll save you money in the long run.
- Design with the End in Mind: Always consider how easy it will be to manufacture, assemble, and test your PCB. Trust me, it pays to think ahead.
- Quality Over Quantity: Investing in quality materials might seem counterintuitive when you’re trying to save money, but it pays off in the long run. Cheap boards are more likely to fail, and that’s a cost you don’t want to incur.
- Be Smart About Project Management: A well-managed project is a cost-effective project. Make sure you’re communicating effectively with your team and keeping an eye on the timeline.
- Speed Is Money: The faster you can get your product to market, the better. It reduces storage costs and gets revenue flowing quicker.
Conclusion
Mastering the art of PCB cost estimation doesn’t have to be complicated. With the formula we’ve shared, you’re now equipped to make more accurate and informed decisions for both prototypes and bulk orders. If you have any questions or need further clarification, don’t hesitate to reach out.
For personalized assistance, feel free to email us at [email protected].