Are you seeking ways to cut costs in your PCB manufacturing process without sacrificing quality? This is a common concern for many customers in the PCB industry. The solution, however, is simpler than you might think.
To achieve cost-effectiveness in your PCB projects, consider these key strategies:
- Simplify Your Design: A complex design not only increases the manufacturing cost but also the probability of errors. Aim for a design that meets your requirements but is as simple as possible.
- Minimize Component Usage: The more components a PCB has, the higher the cost. Try to use fewer components without compromising the functionality of the PCB.
- Standardize Your Design: Using standard sizes and shapes for your PCBs can significantly reduce costs. Non-standard designs often require special tools and processes, which can increase the manufacturing cost.
- Panelize Your Design: Panelization allows multiple PCBs to be manufactured together, which can lead to significant cost savings.
In essence, achieving cost-effectiveness in PCB manufacturing boils down to simplifying and standardizing your design, minimizing component usage, and leveraging panelization. In the following article, we’ll delve deeper into each of these strategies, providing a comprehensive guide to mastering cost-effective PCB manufacturing in China. Let’s get started!
Unpacking the Value of PCB in Electronics Manufacturing
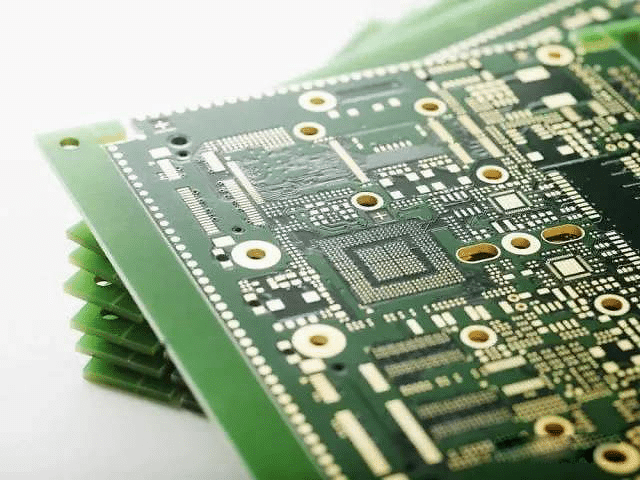
PCB manufacturing is a complex process influenced by a multitude of factors. From exchange rates and utility tariffs to material costs, each aspect plays a role in the final cost of your PCB. Understanding these factors is the first step towards strategic cost reduction.
The User’s Role in Cost Reduction
While some cost factors are beyond control, users have significant influence over others. Strategies for cost reduction include not only the common practices of simplifying the board design, using fewer components, and reducing board complexity, but also exploring innovative design techniques, leveraging advanced software tools, and optimizing the use of materials.
The Power of Proactive Cost Management
Proactive cost management from the earliest stages of board and layout design can lead to significant savings. Once the board is printed, opportunities for cost reduction become limited. Therefore, it’s crucial to implement cost-saving strategies during the design and quoting stages, as well as during assembly.
Embracing Technological Advancements for Cost Reduction
In the era of rapid technological advancements, new opportunities for cost reduction are constantly emerging. From AI-powered design tools to automated manufacturing processes, embracing these advancements can lead to significant cost savings without compromising the final product’s overall performance.
In the following sections, we’ll delve deeper into each of these strategies, providing you with practical tips and insights. So, let’s dive in and revolutionize your PCB manufacturing process!
Designing for Cost-Efficiency: Practical Strategies for Electronics Professionals
When it comes to PCB manufacturing, cost-efficiency doesn’t mean cutting corners. It’s about making smart decisions throughout the design and manufacturing process. Here are eleven practical strategies to help you optimize your PCB designs for cost-efficiency:
1. Minimize PCB Size
Size is a crucial factor in PCB design. Larger PCBs require more materials and take up more space during the manufacturing process, leading to higher costs.
However, making your PCB too small can also increase costs, as it requires precision equipment for assembly. So, striking the right balance is key.
Ensure your PCB has all the necessary components and functionality, but avoid unnecessary increases in size. For instance, a 100mm x 100mm PCB will cost more than a 50mm x 50mm PCB due to the increased material usage.
Remember, the goal is not to make your PCB as small as possible, but to optimize size and complexity to manage costs effectively.
2. Prioritize Quality Materials
Opting for cheaper materials might seem like a good way to cut costs, but this can lead to problems down the line. Low-quality materials can result in PCBs that fail prematurely, leading to higher costs in the long run due to rework or replacement.
Instead of choosing the cheapest option, prioritize quality. For example, using FR-4 material, which is standard and reliable, might cost more upfront than a cheaper alternative, but it will save you money in the long run due to its durability and performance.
3. Stick to Standard Board Shapes
The shape of your PCB can significantly impact manufacturing costs. Non-standard shapes require specialized tools and processes, leading to higher costs.
Unless your design requires a unique shape for a specific reason, it’s generally more cost-effective to stick to standard square and rectangular shapes. A circular or triangular PCB might look interesting, but the additional costs associated with these shapes could outweigh the aesthetic benefits.
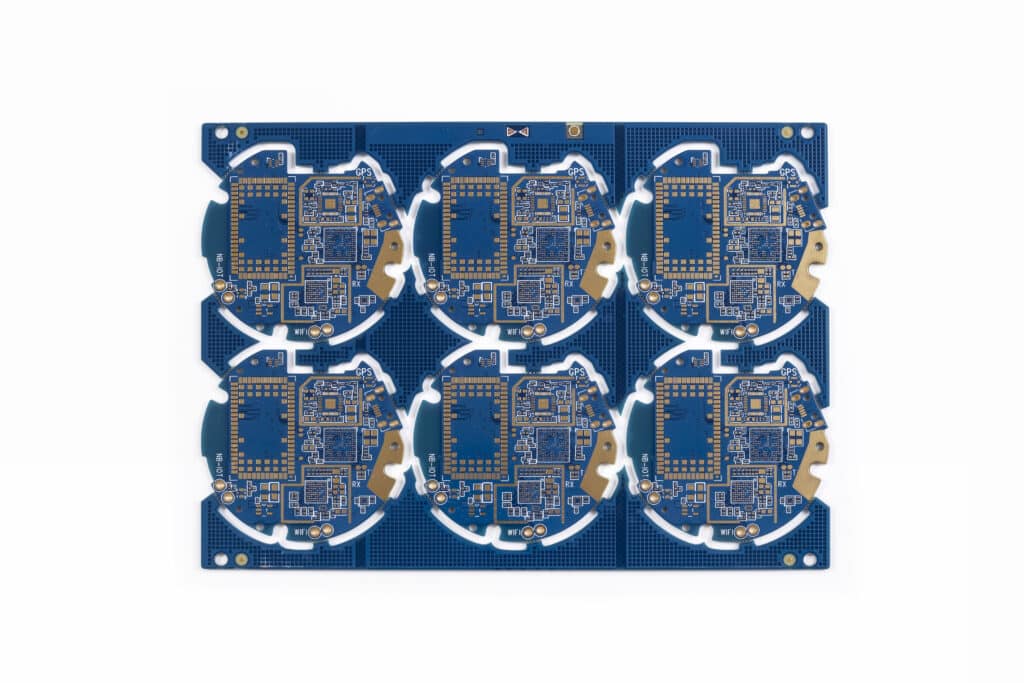
4. Maintain Minimum Spacing Requirements
The spacing between copper objects such as pads and tracks can also affect costs. As spacing decreases, the need for precision machinery increases, leading to higher costs.
Always check with your manufacturer for their specific spacing requirements and design your PCB accordingly. For example, if your manufacturer’s minimum spacing requirement is 0.1mm, ensure that your design adheres to this specification to avoid unnecessary costs.
5. Optimize Hole Diameter
Drilling holes in a PCB isn’t just a matter of punching through the board. The size of the holes matters, and it can significantly impact the cost of your PCB. Smaller holes require precision machinery for drilling, which can increase costs.
So, how do you strike a balance? Aim to use the largest diameter possible for holes to keep costs down, while still meeting your design requirements. For instance, a hole diameter of 0.3mm might be more cost-effective than a 0.1mm hole, as the larger hole can be drilled with less precision equipment.
But remember, don’t compromise the functionality and performance of your PCB for the sake of cost. If your design requires a smaller hole, then it’s a necessary cost.
6. Choose the Right Via for the Design
The type of via used in your PCB design can also impact costs. There are several types of vias, including through-hole, blind, and buried vias.
Through-hole vias are the most common and cost-effective. They go through the entire board, allowing connections between all the layers. On the other hand, blind and buried vias connect only certain layers and require more complex manufacturing processes, making them more expensive.
Unless your design requires high density or high frequency, it’s generally more cost-effective to stick with through-hole vias. For example, a design with 100 through-hole vias might cost less than a design with 50 blind vias and 50 buried vias due to the increased manufacturing complexity of the latter.
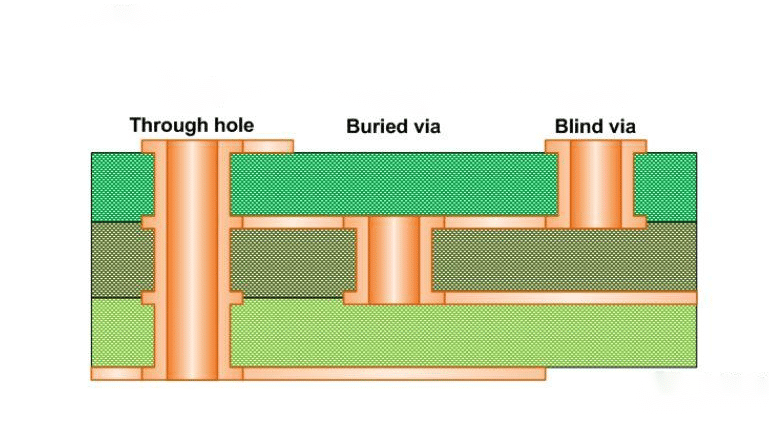
7. Limit Extra Layers
Each additional layer in your PCB design increases the cost, as it requires additional materials and processing. Keep your design as compact as possible and only use as many layers as necessary to meet your design requirements.
For instance, if you’re designing a two-layer PCB, the cost per unit might be around $0.145 for a batch of 1000 units. However, if you can optimize your design to fit into a single-layer PCB, the cost per unit could drop to less than $0.07. That’s a significant cost reduction just by limiting the number of layers in your design. Remember, keep your design as compact as possible and only use as many layers as necessary to meet your design requirements.
8. Optimize Design for Panelization
Panelization is a process where multiple PCBs are grouped together for manufacturing. This not only improves the utilization of board material but also reduces the overall production time, leading to significant cost savings.
For instance, if you have multiple PCB designs that are part of the same project or system, and they are required in the same quantities, instead of manufacturing them individually, you could group these designs together into a single panel. This would reduce the amount of wasted board material and make the manufacturing process more efficient, leading to lower costs.
This strategy is particularly beneficial if you’re working on multiple projects or if you have several small-sized PCBs. By combining these into a single panel, you can achieve economies of scale and significantly reduce your manufacturing costs.
However, it’s important to note that panelization requires careful planning to ensure that the PCBs can be easily separated after manufacturing without damaging the circuits. This involves deciding between methods such as V-groove or ‘V-cut’ and ‘tab-route’ or ‘stamp hole’ for separating the boards. Each method has its own advantages and considerations, and the choice depends on factors such as the board design and the assembly process.
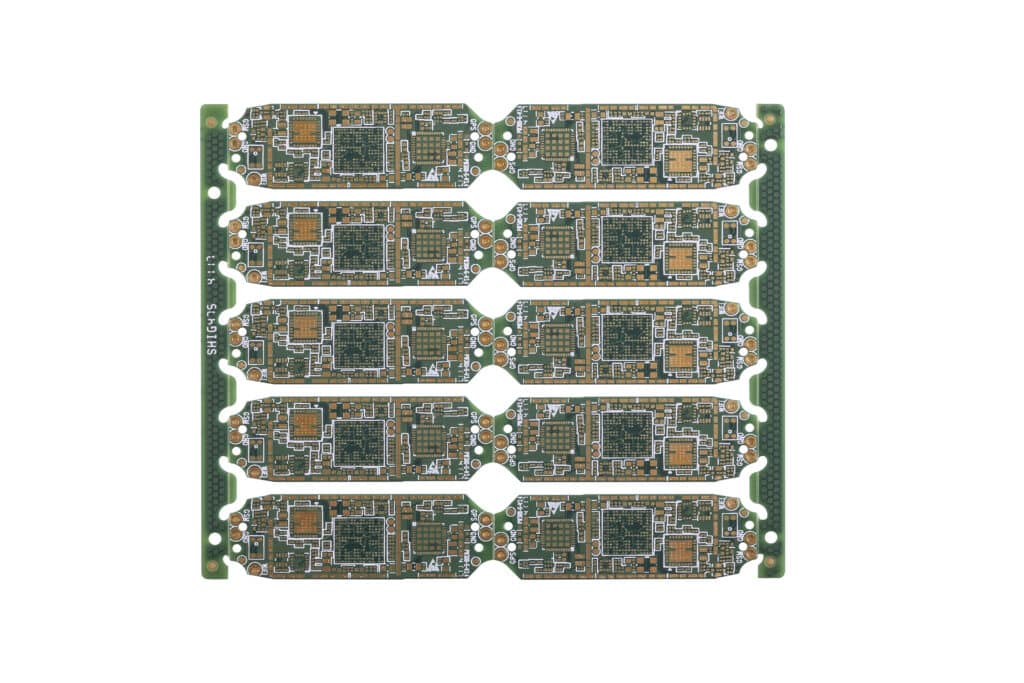
9. Use Industry Standard Sizes and Components
Using standard sizes and components can make the manufacturing process more efficient and cost-effective. Unique components that require manual assembly can drive up costs, so it’s generally best to stick with standard components whenever possible.
For instance, using a 0603 size resistor or capacitor, which is a common standard, would be more cost-effective than using a less common size like 01005. The smaller the component, the more precision is required for placement, which can increase assembly costs.
Similarly, using standard IC packages like SOIC or QFP can be more cost-effective than using less common packages like BGA. The more complex the package, the more complex the assembly process, which can increase costs.
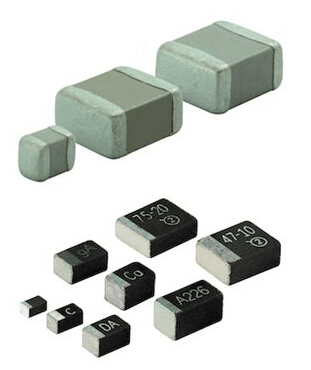
10. Prefer Surface Mount Components
Surface mount technology (SMT) has become the standard for PCB assembly due to its efficiency and cost-effectiveness. Surface mount components can reduce the number of holes needed in your PCB, simplifying the manufacturing process and reducing costs.
SMT components are also generally smaller than their through-hole counterparts, which can help to reduce the size of your PCB. Moreover, the assembly process for SMT is typically faster and less labor-intensive than through-hole assembly, which can lead to further cost savings.
Unless your design is particularly complex or requires the use of specific through-hole components, it’s generally beneficial to opt for surface mount components whenever possible.
11. Design for Manufacturability (DFM)
Design for Manufacturability (DFM) is a design approach that focuses on simplifying the manufacturing process to reduce production costs. This involves considering factors such as the ease of fabrication, assembly, testing, and procurement during the design phase.
For instance, ensuring that components are not placed too close together can make the PCB easier to assemble, reducing the risk of errors and rework. Similarly, using common component values across your design can simplify procurement and potentially reduce costs due to bulk purchasing.
DFM is a broad topic that covers many aspects of PCB design, but the key takeaway is that considering the manufacturing process during the design phase can lead to significant cost savings.
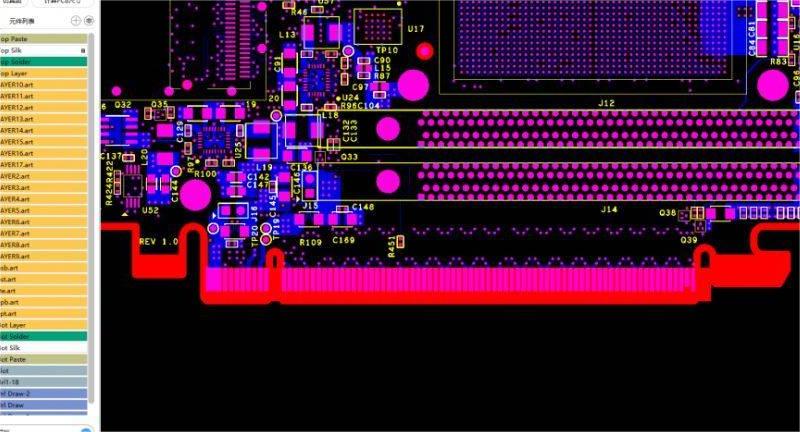
By implementing these strategies, you can significantly reduce the cost of your PCB projects without compromising on quality or performance. Remember, cost-efficiency in PCB manufacturing is not just about reducing costs, but also about maximizing value. With these strategies in hand, you’re well-equipped to design PCBs that are both cost-effective and high-performing.
How Rowsum Reduces PCB and Assembly Cost to a Reasonable Consumer Price
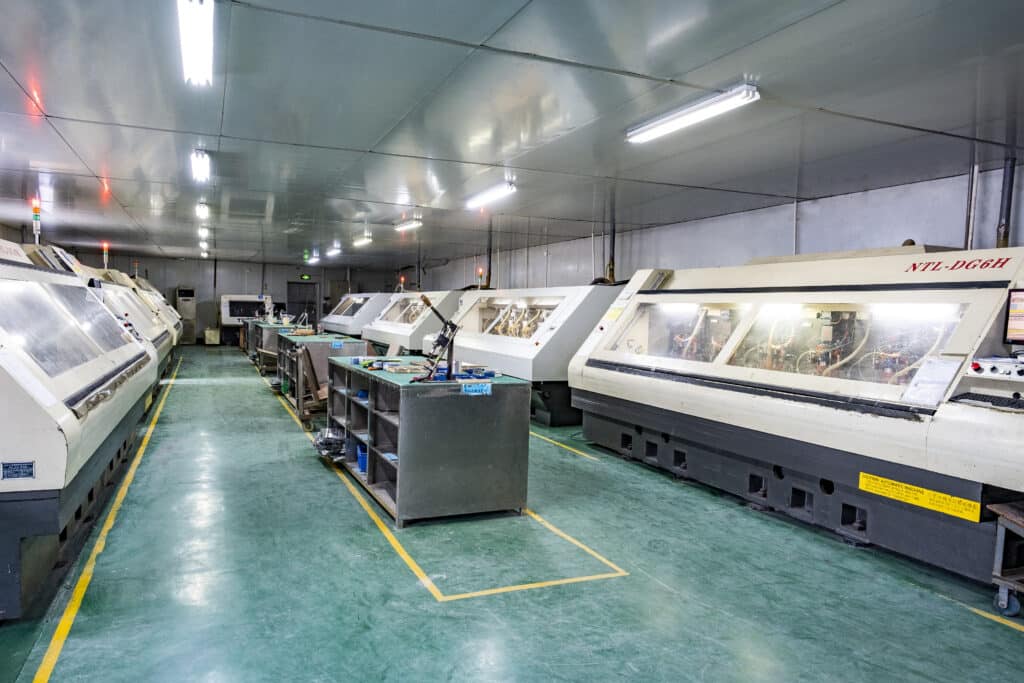
At Rowsum, we’re not just a PCB manufacturer; we’re a partner in your success. We understand the importance of cost-efficiency in PCB manufacturing and assembly, and we’ve tailored our services to deliver high-quality products at competitive prices. Here’s how we do it:
- Direct Factory Pricing
As a direct factory, we eliminate middlemen and pass the savings on to you. Our advanced manufacturing equipment and strict processes ensure the quality of our products, while our 50,000 square meter monthly production capacity allows us to offer unbeatable lead times. This efficiency translates to cost savings for our customers.
- No Minimum Order Requirements
Whether you’re a startup needing small quantities for prototyping or a large corporation requiring mass production, we accommodate orders of any size with no minimum order requirements. This flexibility allows us to cater to businesses of all sizes, helping you manage costs without compromising on your needs.
- Pre-production Advice
Before we start production, we review your design and provide advice on how to optimize it for cost-efficiency. This could include recommendations on board size, layer count, material selection, and more. By catching potential cost issues early, we can help you avoid expensive revisions or rework later on.
- Quality Assurance
Our commitment to quality is backed by numerous certifications, including ISO 9001, ISO 14001, UL, RoHS, and REACH. By prioritizing quality materials and adhering to industry standards, we ensure the longevity and reliability of your PCBs, reducing the risk of costly failures or replacements. This commitment to quality also means fewer production errors, which can lead to significant cost savings.
- Efficient Project Management
Each project is assigned a dedicated project manager for seamless communication and support. This ensures that your specific requirements are met and that any potential issues are promptly addressed, avoiding costly delays or miscommunications. Efficient project management means fewer mistakes and rework, which can significantly reduce costs.
- Global Presence
With offices in the United States and Hong Kong, we provide excellent local service to our international clients. This global presence allows us to respond quickly to your needs, reducing lead times and helping you get your product to market faster. Faster lead times mean faster time to market, which can give you a competitive edge and help reduce storage and holding costs.
- Regular Promotions
We regularly offer promotions for PCB prototypes, providing additional opportunities for cost savings. We believe in growing together with our customers, and these promotions are one of the ways we support your success.
By partnering with Rowsum, you can significantly reduce the cost of your PCB projects without compromising on quality or performance. We’re committed to delivering value at every step of the manufacturing process.
Conclusion: Achieving Cost-Efficiency in PCB Design and Manufacturing
In the realm of PCB manufacturing, cost reduction doesn’t mean compromising on quality. It’s about smart design choices, strategic decisions, and leveraging the right manufacturing processes. The key takeaway from this guide is simple – if it’s not necessary, don’t include it. This principle applies to everything from component selection to board size and shape.
Remember, the goal is to strike a balance between cost and quality. Cutting corners may save you money in the short term, but it could lead to higher costs down the line due to product returns or failures.
If you’re unsure about how to implement these cost-saving strategies, don’t hesitate to reach out to Rowsum. Our team of experts is ready to guide you through the process and ensure your project’s success. Start your journey towards cost-effective PCB manufacturing with us today.