Introduction to PCB Solder Mask
What is it that safeguards the intricate circuitry on a PCB from external factors? How does a PCB prevent soldering elements from merging together and causing a short circuit? These questions lead us to a crucial component of PCB manufacturing – the solder mask.
A solder mask is a protective layer applied to the copper traces of a Printed Circuit Board (PCB). It serves three main functions: protecting the copper from oxidation, preventing solder bridging during the soldering process, and insulating the copper traces to avoid short circuits. Various types of solder masks exist, each with its own application process and use cases.
In the following sections, we’ll delve deeper into the world of solder masks, exploring their purpose, types, application process, and more. This guide is designed to be a valuable resource for PCB manufacturers looking to optimize their production process, as well as for anyone interested in understanding the inner workings of PCBs.
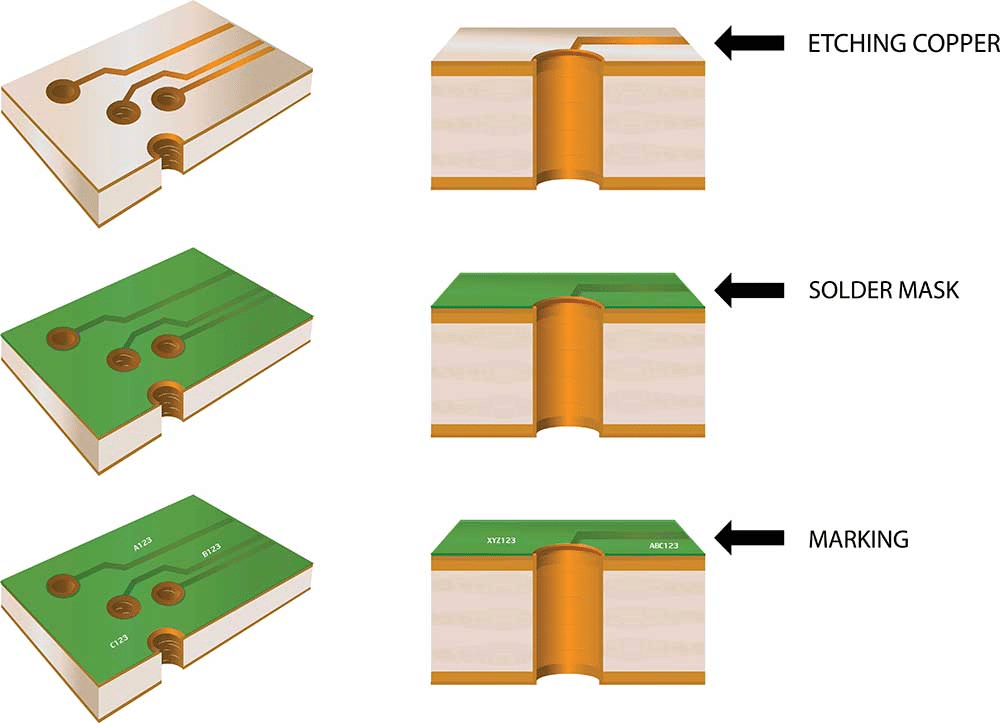
The Crucial Role of Solder Mask in PCB Manufacturing
Solder masks play an integral role in the manufacturing and functionality of PCBs. Their importance can be broken down into five key areas: shielding from oxidation, prevention of solder bridging, insulation of copper traces, enhancement of PCB lifespan, and implications of different solder mask colors.
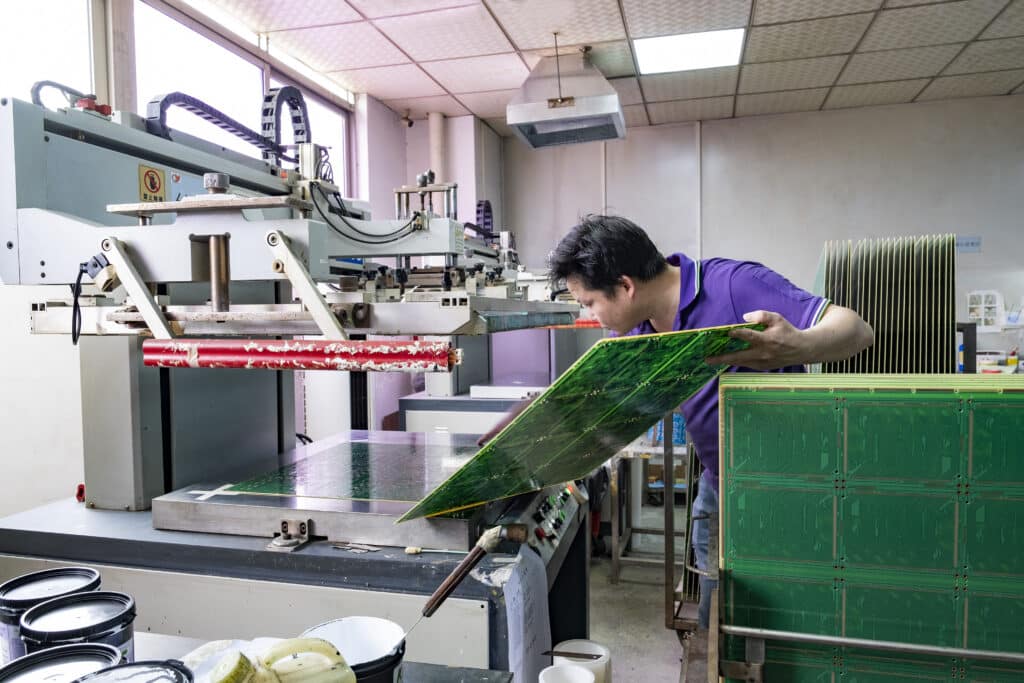
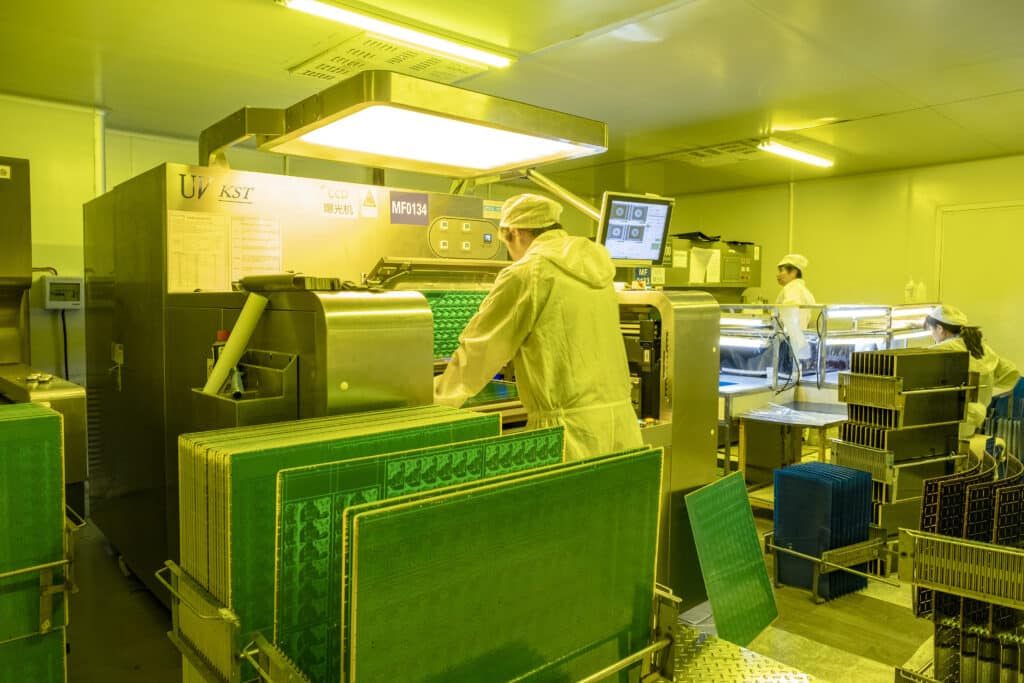
Shielding from Oxidation
The copper traces on a PCB are susceptible to oxidation when exposed to air. Over time, this oxidation can degrade the quality of the copper, affecting the overall performance of the PCB. A solder mask acts as a protective layer, shielding the copper traces from the air and preventing oxidation. This protection is crucial in maintaining the quality and longevity of the PCB.
Prevention of Solder Bridging
During the soldering process, there’s a risk of solder accidentally connecting two adjacent traces, creating a “solder bridge”. This can cause a short circuit, leading to malfunction of the PCB. Solder masks help prevent this by covering the traces, allowing solder to attach only where it’s needed. This precision is crucial in maintaining the functionality of the PCB.
Insulation of Copper Traces
Apart from protection and precision, solder masks also serve as an insulator for the copper traces on a PCB. This insulation is vital in preventing short circuits, ensuring the PCB functions as intended.
Enhancement of PCB Lifespan
A well-applied solder mask can significantly enhance the lifespan of a PCB. The protective and insulating properties of the solder mask contribute to the durability of the PCB, reducing the need for frequent replacements. This is a significant benefit for PCB purchasers, who need their PCBs to last as long as possible to reduce replacement costs and downtime.
Implications of Solder Mask Colors
Solder masks come in various colors, including green, red, blue, black, white, and yellow. The color doesn’t affect the performance of the solder mask, but it can have other implications.
For example, green is often used because it contrasts well with the gold or silver color of the traces, making inspection and troubleshooting easier. Other colors might be used for aesthetic reasons or to differentiate between different PCBs in a complex device.
Specific applications can also influence the choice of solder mask color. For instance, solar panels often use blue or black solder masks to absorb more sunlight. On the other hand, LED light boards might use white solder masks to reflect more light.
By understanding these color implications, you as a PCB purchaser can make more informed decisions. This knowledge empowers you to choose a color that not only meets your functional requirements but also aligns with your aesthetic preferences or branding guidelines.
The Step-by-Step Process of Applying Solder Mask on PCB
Applying a solder mask is a crucial step in PCB manufacturing. It’s a meticulous process that requires precision and expertise. Here, we’ll walk you through the general steps involved in applying a solder mask on a PCB.
1. Cleaning
The first step in the process is to thoroughly clean the PCB. This ensures that the surface is free of any dust, grease, or oxidation that could interfere with the adhesion of the solder mask.
2. Application of Solder Mask
Next, the solder mask is applied to the PCB. The method of application depends on the type of solder mask being used. For instance, a liquid photoimageable solder mask is typically sprayed onto the PCB, while a dry film solder mask is laminated onto the PCB.
3. Curing
After the solder mask is applied, it’s then cured or hardened. This is typically done using heat or ultraviolet light, depending on the type of solder mask. Curing hardens the solder mask and helps it adhere firmly to the PCB.
4. Imaging
Once the solder mask is cured, it’s time for imaging. This involves exposing the solder mask to light that’s passed through a film containing the desired pattern. The light hardens the solder mask in the exposed areas, creating the pattern on the PCB.
5. Developing
The PCB is then placed in a developing solution, which removes the unhardened solder mask from the unexposed areas. This leaves behind the hardened solder mask in the desired pattern.
6. Final Curing
The final step is a second curing process, which fully hardens the solder mask and ensures its adhesion to the PCB. After this step, the PCB is ready for the next stages of the manufacturing process.
Selecting the Right Solder Mask: Key Considerations
While the choice of solder mask is often made by the PCB manufacturer, understanding its implications can help you make more informed decisions. Here are some key points to consider:
1. For Engineers: Pay Attention to the PCB Design
If you’re an engineer, it’s important to specify the areas on the PCB where the solder mask should be applied in your Gerber files. This will ensure that the solder mask is applied correctly during the manufacturing process.
Pay particular attention to areas where components will be soldered. These areas should be free of solder mask to ensure proper soldering. Also, be aware of any areas that require special treatment, such as heat sinks or high-frequency circuits, and communicate these needs clearly to your manufacturer.
2. For PCB Buyers: Confirm the Color
If you’re a PCB buyer, one of the main things you need to confirm with your manufacturer is the color of the solder mask. The color does not affect the functionality of the PCB, but it can have aesthetic implications and can be an important part of your product’s branding.
Moreover, certain types of PCBs typically use specific colors for practical reasons:
- Solar Panels: Solar panels often use blue or black solder masks to absorb more sunlight, enhancing their efficiency.
- LED Light Boards: LED light boards might use white solder masks to reflect more light, improving their brightness.
- Industrial Electronics: In industrial electronics, green is often the color of choice due to its contrast with the gold or silver color of the traces, making inspection and troubleshooting easier.
Understanding these color implications can help you make more informed decisions when ordering your PCBs.
Did You Know? Interesting Facts About Solder Masks
To wrap up our discussion on solder masks, let’s look at some interesting facts that you might not know:
- Why is Green the Most Common Color? The traditional green color of solder masks comes from the use of a specific epoxy known as ‘LPI-Green’. This epoxy was widely used in the early days of PCB manufacturing, and the color stuck. Today, green is still the most common color due to its excellent contrast with copper and silver, making inspection easier.
- Solder Masks in Space: Solder masks play a crucial role in space technology. PCBs used in satellites and spacecraft require high-precision solder masks to withstand the harsh conditions of space, including extreme temperatures and radiation.
- The Smallest Solder Mask Dam: The width of the smallest solder mask dam (the thin line of solder mask that separates two solder pads) can be as small as 75 micrometers, or about the width of a human hair!
- Solder Masks and Art: Some artists use PCBs and solder masks in their artwork. By choosing different colors and patterns, they can create stunning pieces of art.
- UV Light and Solder Masks: Many solder masks are UV-curable, meaning they harden when exposed to UV light. This is a crucial part of the manufacturing process and ensures the solder mask is properly set on the PCB.
These intriguing facts underscore the fascinating world of solder masks and their integral role in PCB manufacturing.
Conclusion
Solder masks are a vital yet often overlooked component of PCBs, influencing their durability, functionality, and aesthetics. Understanding their role can help anyone involved in the electronics industry make more informed decisions.
If you’re in search of a reliable partner for your PCB needs, Rowsum is your go-to solution. As a leading PCB&PCBA manufacturer, Rowsum delivers high-quality products tailored to your specifications. For more information or to start your project, reach out to us at [email protected].
Remember, the choice of solder mask can significantly impact your PCB. Make sure to communicate your needs clearly to ensure the final product aligns with your expectations.