Introduction
Have you ever wondered why your electronic devices work so seamlessly? The secret lies in the heart of these devices – the Printed Circuit Board (PCB), and more specifically, the solder used to connect the various components on the PCB. Choosing the right solder for your circuit board is a crucial decision that can significantly impact the performance and longevity of your electronic devices.
So, what is the best solder for a circuit board? How do you choose the right one? The answer is not as straightforward as you might think. The best solder for your circuit board depends on various factors, including the type of components you’re using, the temperature at which your device operates, and even environmental considerations.
The best solder for most general applications is a lead-based solder with a composition of 60% tin and 40% lead (60/40), known for its low melting point and strong electrical conductivity. However, due to health and environmental concerns, many industries are shifting towards lead-free solders, such as those made from a tin-copper (SnCu) or tin-silver-copper (SAC) alloy.
In this article, we’ll delve deeper into the world of solders, exploring the different types of solders available, their pros and cons, and how to choose the right one for your specific needs.
Understanding What Solder Is
In the realm of electronics, solder is the critical link that ensures all components function harmoniously on a circuit board. It’s a fusible metal alloy that, when melted, forms a conductive path, ensuring your device operates as intended.
The history of soldering dates back to 4000 BC, where it was used in making jewelry, tools, and stained glass. Today, it’s an integral part of our digital world. Just think about it – the device you’re using to read this article wouldn’t work without solder!
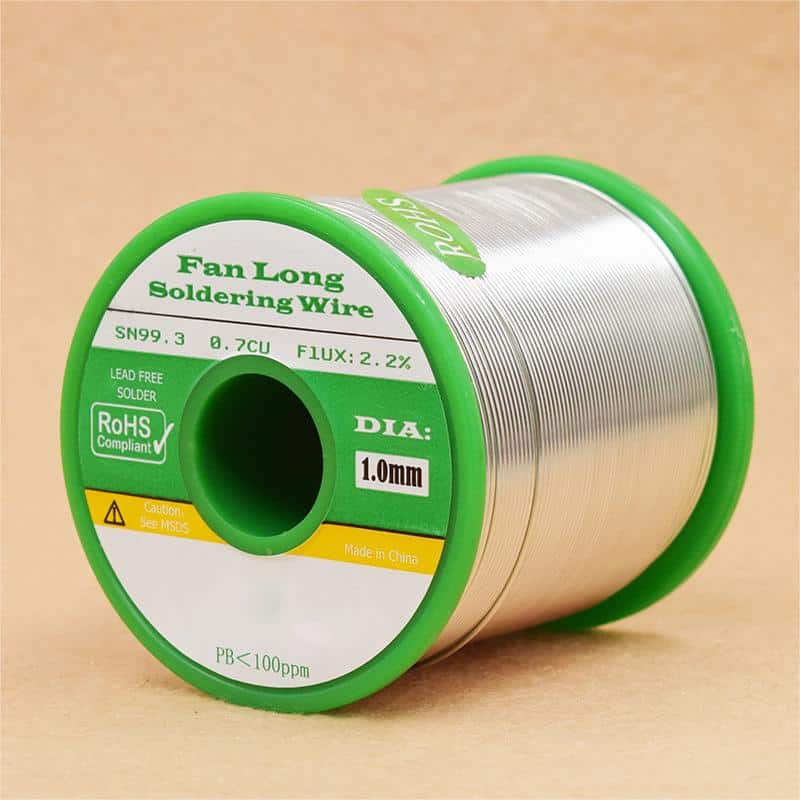
Lead-based Solder
Lead-based solder has been a mainstay in the electronics industry for decades. It’s a mix of tin (Sn) and lead (Pb), usually in a 60/40 or 63/37 ratio. This type of solder melts at around 183-190°C (361-374°F), making it easy to work with. It’s known for its excellent electrical conductivity, ensuring efficient performance of the circuit board.
But remember, lead is a toxic metal. Prolonged exposure can lead to serious health issues, including neurological damage. Moreover, improper disposal of lead can harm the environment, contaminating soil and water. So, if you’re using lead-based solder, make sure to handle and dispose of it responsibly!
Lead-free Solder
As the electronics industry seeks safer alternatives, lead-free solder has emerged as a viable option. These solders are made from alloys like tin-copper (SnCu) and tin-silver-copper (SAC). They have a higher melting point than lead-based solders, typically around 217-227°C (423-441°F), requiring adjustments in the soldering process.
But here’s the twist – lead-free solders, especially those containing silver, can offer better mechanical strength and thermal fatigue performance than lead-based solders. Plus, they’re safer and more environmentally friendly, aligning with the growing emphasis on sustainability. So, if you’re looking to make a green choice, lead-free solder might be the way to go!
Silver Alloy Solder
For those seeking top-tier performance, silver alloy solder stands out. Known for its high electrical conductivity, it’s often used in high-performance applications where superior signal integrity is required.
Silver solder typically contains 2-4% silver and has a melting point of around 217-221°C (423-430°F). It’s able to withstand high temperatures, making it an excellent choice for devices operating under extreme conditions. However, this superior performance comes with a higher price tag due to the cost of silver. So, if you’re working on a high-end project and budget isn’t a concern, silver alloy solder could be your best bet.
Factors to Consider When Choosing Solder for Circuit Boards
Choosing the right solder for your circuit board is not a one-size-fits-all scenario. It’s a decision that should be made based on several factors, each playing a crucial role in the performance and longevity of your electronic device. Let’s delve into these factors:
Type of Project
The nature of your project plays a significant role in the type of solder you should choose. Are you working on a high-performance device that operates under extreme conditions? If so, a silver alloy solder might be your best bet due to its high electrical conductivity and temperature resistance.
On the other hand, if you’re working on a standard electronic device, a lead-based or lead-free solder could be suitable. Remember, lead-based solder is easier to work with due to its lower melting point, but lead-free solder is safer and more environmentally friendly. It’s all about finding the right balance for your specific project.
Materials Being Soldered
The materials you’re soldering also influence the type of solder you should use. For instance, silver alloy solder is ideal for silver-coated materials due to its excellent wetting properties.
On the other hand, lead-free solder, particularly tin-copper (SnCu) and tin-silver-copper (SAC) alloys, work well with a variety of materials, making them a versatile choice. So, take a moment to consider the materials you’ll be working with before making your decision.
Wire Size
The size of the solder wire you choose can also impact your soldering process. Thinner wires are generally better for precision work on smaller components, while thicker wires can be more suitable for larger components or joints. It’s important to match the wire size with the scale of your project for optimal results.
Flux
Flux plays a pivotal role in the soldering process. It’s a chemical cleaning agent that prepares the metal surfaces for soldering by removing oxidation and other contaminants. This is crucial because clean, oxide-free surfaces ensure a strong, electrically conductive bond when soldered.
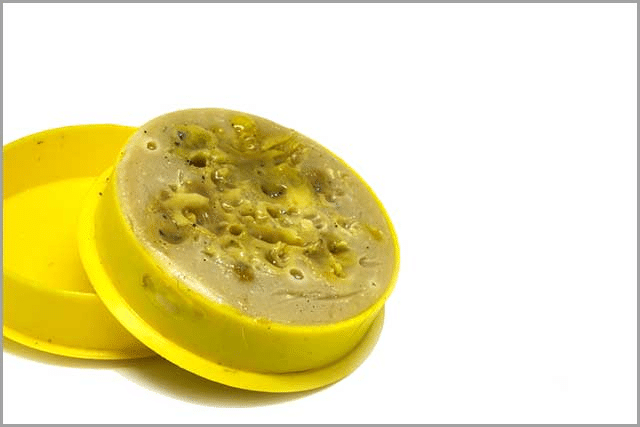
There are different types of flux, each with its own characteristics:
- Rosin Flux: This is the most common type of flux used in electronics. It’s derived from pine sap and is non-corrosive, meaning it won’t damage the components or the board. However, it leaves a sticky residue that needs to be cleaned after soldering.
- Water-Soluble Flux: As the name suggests, this flux can be cleaned off with water. It’s more aggressive than rosin flux, making it suitable for metals that are harder to solder. However, its residue is corrosive and must be thoroughly cleaned after soldering.
- No-Clean Flux: This type of flux leaves a residue that is non-conductive and non-corrosive, eliminating the need for post-soldering cleaning. It’s ideal for sensitive electronics where cleaning could potentially cause damage.
Some solders come with a flux core, which melts during soldering, cleaning the joint area. This can make the soldering process easier, especially for beginners. However, in some cases, you might need to apply flux separately, especially when working with larger components or when reworking soldered joints.
Environmental Impact
If you’re environmentally conscious, you might want to opt for lead-free or silver alloy solder. These types of solder are less harmful to the environment compared to lead-based solder. Remember, every choice we make impacts our planet, and choosing environmentally friendly solder is one way to reduce that impact. It’s a small step, but every little bit helps, right?
Regulatory Requirements, Cost, Reliability, Availability, and Health and Safety
Don’t forget to consider regulatory requirements, cost, reliability, availability, and health and safety. Depending on your region, there may be regulations that restrict the use of certain types of solder. The cost of solder can also be a deciding factor, especially if you’re working on a budget. And of course, the reliability and availability of the solder type are crucial considerations. Last but not least, always prioritize your health and safety when working with solder, especially lead-based ones.
Practical Tips When Selecting the Right Solder
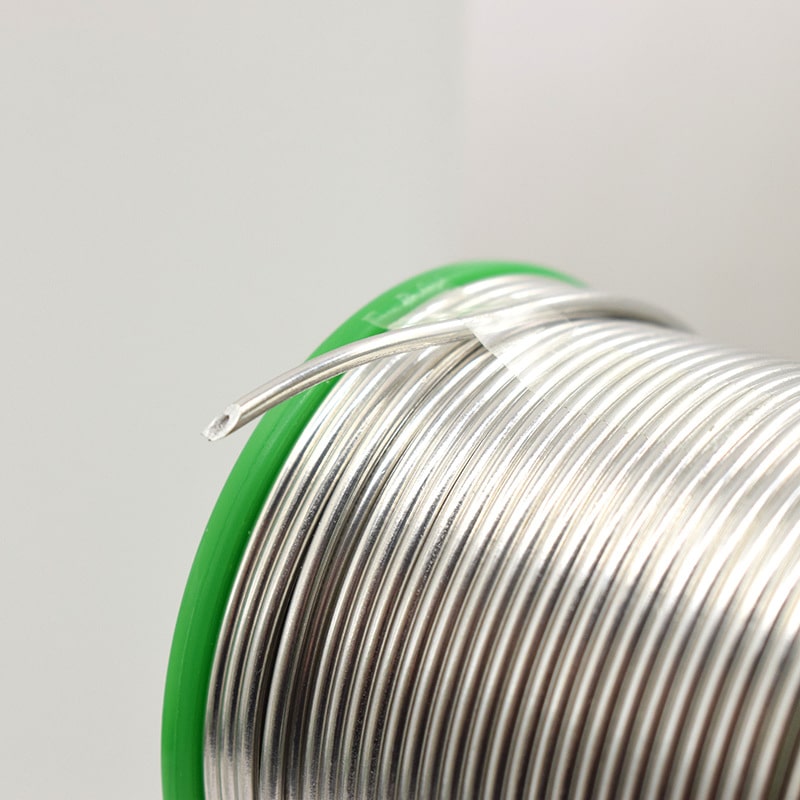
Selecting the right solder is a crucial step in ensuring the success of your soldering project. Here are some practical tips that can help you make the right choice and avoid common mistakes:
- Experiment with Different Types of Solder
Every soldering project is unique, and what works best for one might not work as well for another. Don’t be afraid to experiment with different types of solder (lead-based, lead-free, silver alloy) on scrap materials to see which one suits your project best. This hands-on experience can provide valuable insights that you won’t get from reading product descriptions alone.
- Pay Attention to the Solder Diameter
The diameter of the solder wire can significantly impact your soldering process. For precision work on small components, a thinner solder wire is usually more manageable. On the other hand, a thicker wire might be more suitable for soldering larger joints. Always consider the scale of your project when choosing the solder diameter.
- Keep Your Soldering Tools in Top Shape
The condition of your soldering tools can directly affect the quality of your soldering joints. Keep your soldering iron tip clean for optimal heat transfer and to prevent contamination. Regular maintenance of your tools can lead to better soldering results.
- Store Your Solder Correctly
Proper storage of your solder can help maintain its quality over time. Keep your solder in a cool, dry place to prevent oxidation. Also, try to handle the solder wire as little as possible to avoid contamination from skin oils.
- Use the Right Amount of Flux
Using the right amount of flux can make a big difference in your soldering process. Too much flux can leave a messy residue, while too little might not clean the joint adequately. Practice applying flux to achieve the right balance.
- Prioritize Safety
Soldering can pose certain risks if not done safely. Always work in a well-ventilated area to avoid inhaling potentially harmful fumes. Wear safety glasses to protect your eyes, and if you’re using lead-based solder, make sure to wash your hands thoroughly after soldering.
H2: Conclusion
Choosing the right solder for your circuit board is a critical decision that can significantly impact the performance and longevity of your electronic device. It’s not just about picking the most expensive option or the one with the most features. It’s about understanding your project’s specific needs and finding a solder that meets those requirements.
At Rowsum, we understand the complexities of this decision. That’s why we’re committed to providing high-quality PCB products and services that cater to a wide range of needs. Whether you’re looking for PCB manufacturing, PCB assembly, or components sourcing, we’ve got you covered.
We invite you to explore our services:
If you have any questions or need further assistance, feel free to reach out to us at [email protected]. We’re here to help you make the right choices for your project.