Introduction
Ever held your smartphone in your hand and wondered, “How do they fit so much into such a small device?” I know I have. The secret to this marvel of compactness and functionality lies in the heart of these devices – the circuit boards. But not just any circuit boards, we’re talking about Semi-Flex FPCs.
Semi-Flex FPCs, or Semi-Flexible Printed Circuit Boards, are a game-changer in the electronics industry. These circuit boards are not only flexible but also incredibly thin, allowing for more compact and efficient device designs. In a nutshell, Semi-Flex FPCs are the key to creating smaller, more powerful electronic devices that we use in our daily lives.
So, if you’re as curious as I am about how these amazing devices work, stick around as we delve deeper into the world of Semi-Flex FPCs, their advantages, and why they’re becoming the go-to choice for modern electronic devices.
Understanding Semi-Flex FPCs
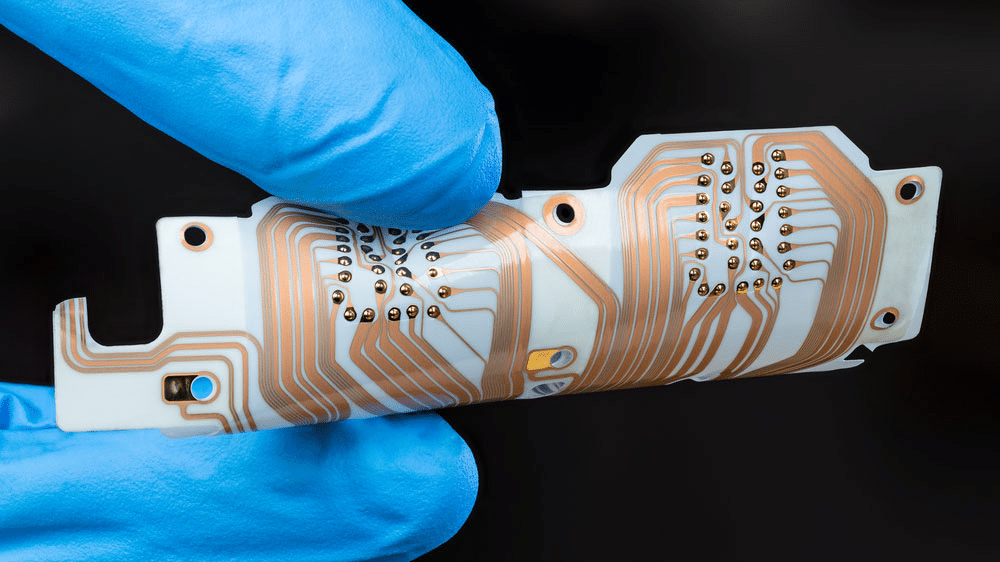
Semi-Flex FPCs are a unique type of circuit board that combines the best of both worlds – the rigidity of traditional Printed Circuit Boards (PCBs) and the flexibility of Flexible Printed Circuit Boards (FPCs). But how does this work?
A Semi-Flex FPC is designed to be flexed during installation but remains rigid during operation. This is achieved by using a special type of material that can withstand bending and folding without causing damage to the circuitry. This material is typically a type of plastic, such as polyimide, that is both flexible and durable.
The real magic of Semi-Flex FPCs lies in their construction. They are made up of several layers, including a base material, a conductor, and a protective coverlay. These layers are bonded together using a special adhesive that can withstand the heat generated by the electronic components and the bending and folding of the FPC.
The result is a circuit board that is not only compact and lightweight but also highly durable and flexible. This makes Semi-Flex FPCs an ideal choice for applications where space and weight are critical considerations, such as in smartphones, wearable devices, and medical equipment.
The Composition of a Semi-Flex FPC
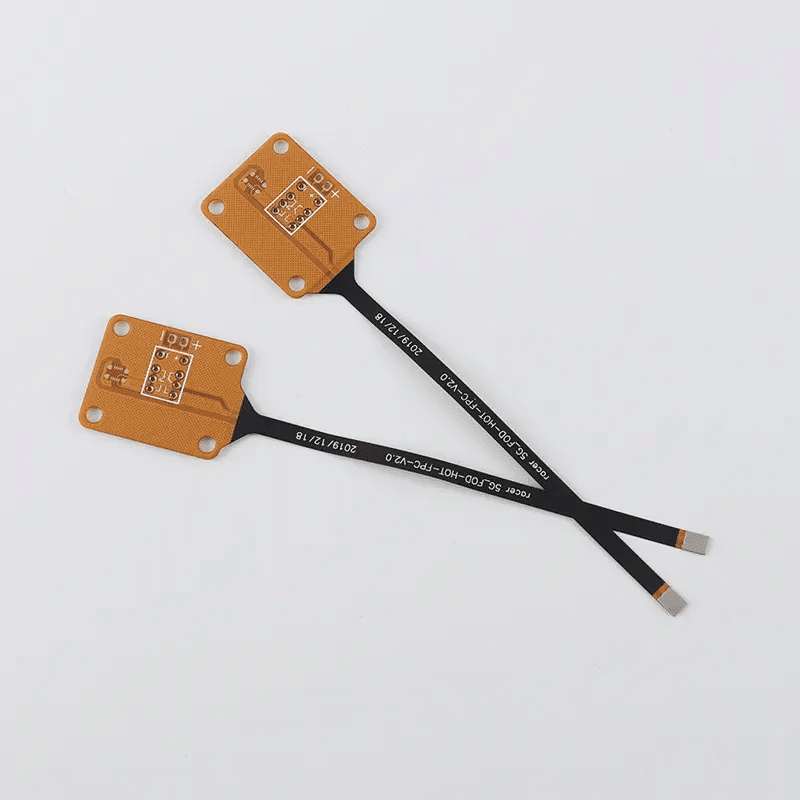
What makes a Semi-Flex FPC so flexible and durable? The answer lies in its unique composition. Let’s peel back the layers and take a closer look:
The Base Material: The Heart of Flexibility
At the core of every Semi-Flex FPC lies its base material, typically a high-performance polymer like polyimide. This isn’t your everyday polymer. It’s a material engineered to endure the harshest of electronic applications, a material that stands strong in the face of high heat and mechanical stress.
Polyimide is chosen for its exceptional mechanical properties and thermal stability. It can withstand temperatures of up to 260°C, making it a reliable choice for applications that involve high heat. Moreover, polyimide also has excellent electrical properties, including a high dielectric strength and low dielectric constant, which are crucial for the efficient operation of the circuit.
But the standout feature of polyimide is its flexibility. It can bend, twist, and flex without breaking or losing its electrical properties. This flexibility opens up new possibilities in electronic design, allowing the Semi-Flex FPC to conform to the shape of the device it’s installed in.
The Conductor: The Lifeline of Connectivity
Next up is the conductor layer, the lifeline of a Semi-Flex FPC. This layer is typically composed of a thin layer of copper. But this isn’t just any metal. It’s a highly conductive material, chosen for its ability to efficiently carry electrical signals from one component to another.
The copper layer is etched with micron-level precision to create intricate circuit patterns. These patterns are the heart of the FPC, directing the flow of electricity where it’s needed. It’s like a network of tiny roads, guiding the traffic of electrical signals through the circuit.
But what truly sets the conductor layer apart is its thinness. Despite being only a few microns thick, it can carry enough current to power complex electronic devices. This is what gives the Semi-Flex FPC its defining characteristic – the ability to pack a lot of functionality into a small space.
The Coverlay: The Protective Shield
The coverlay is the protective shield of a Semi-Flex FPC, typically composed of the same material as the base, such as polyimide. This isn’t just any protective layer. It’s a specially engineered barrier, designed to safeguard the delicate conductor layer from environmental threats.
The coverlay serves as a first line of defense against potential damage from moisture, dust, and physical impact. It’s like an invisible force field, keeping the harmful elements at bay and ensuring the longevity and reliability of the FPC.
But what truly sets the coverlay apart is its flexibility. Despite being a protective layer, it doesn’t compromise the flexibility of the FPC. It bends and flexes along with the base material and conductor, maintaining the FPC’s shape and functionality even under stress.
The Adhesive: The Unsung Hero
The final layer of a Semi-Flex FPC is the adhesive, often overlooked but absolutely crucial. This isn’t just any adhesive. It’s a specially formulated compound, designed to bond the base material and the conductor layer together.
The adhesive layer is designed to withstand the thermal stress and mechanical deformation that the FPC undergoes during its lifecycle. It’s like the glue that holds our world together, quite literally, ensuring the structural integrity of the FPC.
But what truly sets the adhesive apart is its resilience. Despite being subjected to high temperatures and constant flexing, it maintains its bonding strength. It’s the silent hero that holds everything together, ensuring that the Semi-Flex FPC can perform its function reliably and efficiently.
And there you have it – the unique composition of a Semi-Flex FPC. Each layer plays a crucial role, working together to create a flexible, durable, and efficient solution for electronic design.
The Difference Between FPC and PCB
When it comes to choosing the right circuit board for your project, understanding the differences between FPC (Flexible Printed Circuit) and PCB (Printed Circuit Board) is crucial. These differences can impact cost, performance, and the overall success of your project.
Flexibility and Form Factor
The most significant difference between FPCs and PCBs lies in their physical properties. FPCs, especially Semi-Flex FPCs, are known for their flexibility. They can bend, twist, and flex to fit into tight spaces and adapt to various shapes. This characteristic makes them ideal for modern electronic devices that require components to fit into unconventional spaces.
On the other hand, PCBs are rigid and robust. They provide a solid platform for electronic components and are typically used in devices where flexibility is not a requirement.
Cost Implications
While FPCs offer unique advantages, they can also be more expensive to produce than traditional PCBs due to their complex manufacturing process. However, the higher upfront cost can be offset by the potential savings in device size, weight, and overall performance.
Durability and Performance
FPCs are designed to withstand bending and flexing, making them more durable in certain applications. They also offer better heat dissipation, which can enhance the performance and lifespan of your electronic components.
PCBs, while less flexible, are known for their robustness and can support heavier components and larger circuit designs.
Applications and Use Cases
FPCs and PCBs also differ in their typical applications and use cases. Due to their flexibility and heat management capabilities, FPCs are often used in compact and heat-intensive devices such as smartphones, laptops, and wearable technology.
PCBs, with their robustness and rigidity, are commonly found in larger electronic devices such as desktop computers, televisions, and home appliances.
In conclusion, while both FPCs and PCBs play crucial roles in the electronics industry, their unique characteristics make them suitable for different applications. Understanding these differences can help you make an informed decision when choosing between an FPC and a PCB for your next project.
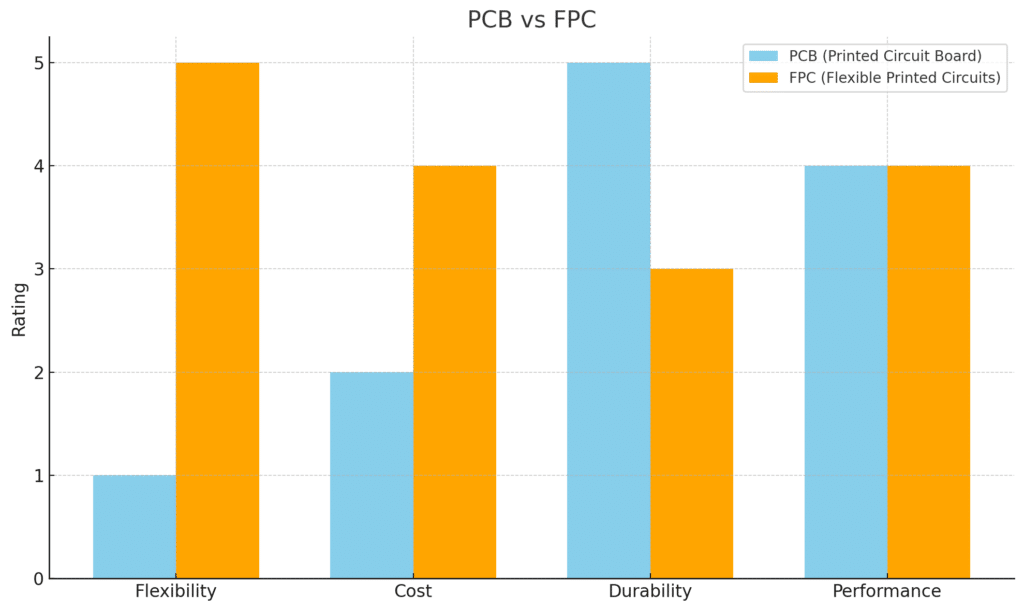
The Future of Semi-Flex FPCs: Actionable Strategies for Innovation
The future of Semi-Flex FPCs is ripe with opportunities for those willing to innovate and adapt. Here are some concrete strategies that you can implement today to stay ahead of the curve:
Embrace Component Miniaturization
As devices continue to shrink, engineers must adapt their designs to accommodate smaller components. This not only saves space but also reduces weight, which can be crucial for portable devices or wearables.
Tip: Start by identifying components in your design that have smaller, equivalent alternatives. For instance, if you’re currently using a 0603 package resistor, consider switching to a 0402 or even 0201 package if your manufacturing process allows it. This could save significant space on your FPC, allowing for more compact and lightweight designs.
Invest in Thermal Management Solutions
As Semi-Flex FPCs become more complex, managing heat dissipation is increasingly important. Effective thermal management can prevent overheating, improving the reliability and lifespan of your device.
Tip: Incorporate thermal vias into your design. Thermal vias are small holes in the PCB that are filled with a thermally conductive material, allowing heat to dissipate more effectively. Place thermal vias under heat-generating components like power ICs. Use thermal simulation software to identify these areas. For instance, a thermal resistance of less than 10°C/W is often a good target for most designs.
Optimize Your Design for Flexibility
As the demand for flexible electronics grows, optimizing your design for flexibility can give you a competitive edge. Flexible designs can conform to various shapes and are more resistant to mechanical stress, reducing the risk of failure in harsh environments.
Tip: Use serpentine traces in areas of the FPC that need to bend. Serpentine traces are traces that meander back and forth, allowing the FPC to bend and flex without damaging the traces. Be sure to maintain a consistent trace width to prevent impedance mismatches. For instance, a trace width of 0.15mm is often a good starting point for most designs.
By implementing these strategies, you can create Semi-Flex FPCs that are more compact, reliable, and adaptable, meeting the demands of the future head-on. Remember, the future isn’t just about following trends – it’s about actively shaping them.
Conclusion
In the realm of electronics, Semi-Flex FPCs are not just components; they are the embodiment of flexibility meeting functionality, a testament to the power of innovative engineering. They are the key that unlocks design possibilities, bending and twisting to the will of the creator, while maintaining their core purpose – to transmit electrical signals reliably and efficiently.
At Rowsum, we believe in the power of these flexible marvels and are committed to helping you harness their full potential. Whether you’re looking to manufacture a Semi-Flex FPC, assemble a complex electronic device, or source components for your next project, we have the expertise and resources to make it happen.
Explore our services:
We’d love to hear from you. Email us at info@rowsum.com and let’s start a conversation about how we can shape the future of electronics together.